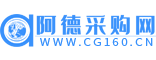
价格:面议
0
联系人:戴生
电话:
地址:东莞市 厚街镇桥头管理区
产品规格:
产品数量:
包装说明:
关 键 词:MIM牙齿矫形托槽
行 业:
发布时间:2007-06-27
金属射出成形(MIM)--复杂精密零件生产工艺与主要产品 金属射出成形(MIM)--针对复杂精密零件,低成本、**新型加工方式。金属射出成形,是一种将金属粉末与高分子黏结剂混合,使其在加热后具有类似塑料材料的流动性,而可藉由一般射出成形机制造出**尺寸及复杂形状的零件,射出成形后的生胚再经过脱脂过程以去除高分子黏结剂与烧结后可得到高密度且具有优异机械与物理性质的烧结零件。 在过去十余年,在美日等**地区中已成为**发展的制造业。目前已广泛地应用于制造各种复杂形状的零件如计算机用散热片、手工具零件、针车零件、工具机零件、汽机车零件、OA事务机器零件、钟表眼镜用零件、医疗器材零件等。而且材料适用性广,可广泛应用于常用有色金属,不锈钢,钛合金,硬质合金,贵金属等。 金属射出成形优点: 降低成本 广泛的产品外型尺寸及设计 精密误差(+/- 0.5%) 良好尺寸控制 各种合金、混合及特性材料的广泛应用 可适用精密复杂的几何物体 高材料密度及强度 弹性化设计 制造良好表面抛光等。 金属射出成形适用领域: 航空工业 飞机机翼绞链、火箭喷嘴、导弹尾翼、陶瓷涡轮叶片芯子 汽车工业 点火控制锁部件、涡轮增压器转子、阀门导轨部件、汽车刹车装置部件、汽车防晒棚部件 电子工业 磁盘驱动器部件、电缆连接器、电子管壳、计算机打印头、电子封装件、热沉材料 **工业 地雷转子、枪板扳机、穿甲弹弹心、准星座、集束箭弹小箭 医疗器械 牙齿矫形托槽、体内缝合针、活体组织取样钳、防辐射屏罩 日用产品 表壳、表带、表扣、高尔夫球头和球座、运动鞋扣、体育枪械零件、文件装订打孔器 机械行业 异形铣刀、切削工具、微型齿轮 常用产品如: 笔记型计算机零件 ( LCD 支撑架及基座) :材质 : SS316L 及 17- 4PH , (取代精密 铸造或锻造件) 锁芯: 材质 : 17-4PH 或 Fe-8% Ni 镀铬 (取代精密铸造) 手工具零件: 材质 : 高速钢 M2, 低碳合金钢 (取代粉末冶金及精密铸造) 气动, 电动工具零件:材质 : 高速钢 M2, 低碳合金钢 缝纫纺织机零件: 材质 : 高速钢 M2 (取代机械加工制品) SMT自动插件机零件: 材质 : 低碳合金钢镀铬 (取代机械加工或精密铸造制 线性滑轨, 滑块: (自动化及机器手臂零件) 材质 : 高速钢 M2 或工具钢镀铬(取代机械加工制品) *军火零件类: (取代精密铸造零件) 铰链(3C类Hinge)等 MIM Technology Metal Injection Molding (MIM) technology combines the shape making capabilities of plastic injection molding with the material flexibility of powder metallurgy. Taking advantage of unique process capabilities, it allows one complex geometry or co-molding and bonding dissimilar materials. Combining fine metal powders with a “binder” system, components are injection molded, de-bound and sintered, resulting in high-density, complex, precisely-shaped parts exhibiting properties approaching that of wrought material. Alloy and stainless steel, as well as other non-ferous alloys such as titanium, are common materials for MIM. MIM is used by many industries , such as medical device, telecom, electronics and automotive parts manufacturers, and is a viable and cost effective alternative to other types of metal processes, such as machining and casting. The MIM process is particularly well suited for the high-volume manufacture of relatively small, complex components requiring high strength, high performance and cost efficiency. MIM Process The MIM process mainly consists of 4 steps. 1. FEEDSTOCK. The metal powder is mixed with thermoplastic binders to produce a homogeneous feedstock; with approximately 60 volume % metal powder and 40 volume % binders. 2. INJECTION MOLDING. The feedstock is placed into an injection molder and molded to form a net shape green part. Injection molding occurs at relatively low temperatures and pressures inconventional plastic injection molding machines. The molds are similar to those used for plastic injection molding including slides and multi-cavity configurations. 3. DEBINDING. After injection molding , the binder is removed from the green part via an evaporative process called “debinding”. 4. SINTERING. After debinding the part is sintered to form a high-density metal part.Sintering occurs at high temperatures, up to 1260 °C (2300 °F), near the melting point of the metal; under a dry H2 atmosphere or inert gas atmosphere. During sintering, the part will shrink isotropically to form a dense shape. Since, the complex shape of the molded part is retained through the process, close tolerances in the as-sintered part can be achieved. Scrap is eliminated or significantly reduced since machining of the part after sintering is usually not necessary. Certainly, the sintered part can be processed with heat treatment, machining or other means to achieve some special performance. Advantages of MIM Complexity - Geometries comparable to plastic injection molding Density - Typically =95% Surface Finish - As processed 32ms or better Alloy Selection - Many ferrous, nickel-based and copper-based alloys available Stable Quality - Efficient mass production Mechanical Properties Comparable to wrought alloys of similar composition Cost Effective - Conserving over 20% typically, also shorter lead time Typical Mechanical Properties of MIM Alloys Material Designation Code Density Hardness Tensile Strength Elongation g/cm3 HR Mpa % Low Alloy Stele MIM-2200 (As-sintered Condition) 7.65 45HRB 290 40.0 MIM-2700 (As-sintered Condition) 7.65 69HRB 440 26.0 MIM-4605 (As-sintered Condition) 7.62 62HRB 415 15.0 MIM-4605 (Heat Treated Condition) 7.62 48HRB 1655 2.0 Stainless Steel MIM-316L (As-sintered Condition) 7.92 67HRB 520 50.0 MIM-17-4PH (As-sintered Condition) 7.50 27HRB 900 6.0 MIM-17-4PH (Heat Treated Condition) 7.50 40HRB 1185 6.0 MIM-430L (As-sintered Condition) 7.50 65HRB 415 25.0 Tungsten Alloy 95%W-Ni-Fe 18.10 25HRB 960 25.0 97%W-Ni-Fe 18.10 30HRB 940 15.0 Hard Alloy YG8X 14.90 HRA90 (Transverse Rupture Strength)2300 / Soft Magnetic Alloy MIM-2200 7.60 / 290 40.0 MIM-Fe-50%Ni 7.70 / 455 30.0 MIM-Fe-3%Si 7.45 / 530 24.0 MIM-Fe-50%Co 7.70 / 205 <1.0 MIM-430L 7.50 / 415 25.0 Application Automotive Industry Electronics and Telecom Medical Devices Firearms Industry Consumer Products Mechanical Industry Tools More Applications ignition ontrol module hard disc drive parts orthodontic brackets small arms parts watchcase cutting tool drillstock precision valve airbag sensor module electronic packaging radiation protection shield armour-piercing bullet core watch chain micro gear wheel arc tooth pump brake component printing head surgical scalpel high energy bullet watch hammer special three-dimensional parts blade clamp mold core turbo heat sink material implanted devices golf head cover coupling device ...... magnet sensor seat cable connector fishing gear parts multifunctional tool pressure control & flowmeter component of fuel injection system mobile phone hinge lock parts pothook of driving system laptop hinge engine rocker mobile phone crust oxygen sensor of engine management system micro motor parts cruise sensor seat