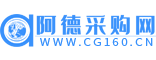
时间:2020-11-16 09:57:36 点击:809
回转支承承载能力 影响回转支承承载能力的四个参数 回转支承的失效形式有两种,一是滚道损坏,二是断齿,而滚道损坏占的比例达98%以上,因此我们说,滚道质量是回转支承质量的中心问题,影响回转支承滚道质量的因素较多,其中滚道淬火硬度、淬硬层深度、滚道曲率半径和接触角无疑是较重要的四个影响因素,它们以不同的方式影响着滚道质量,并决定了回转支承的承载能力和使用寿命。 *滚道硬度 回转支承滚道淬火硬度对其额定静容量影响较大,如以HRC55时额定静容量为标准1,则滚道硬度与额定静容量有下列对应关系: 标准规定的较低硬度为HRC55,通常实际平均淬火硬度在HRC57左右,因此绝大多数回转支承实际承载能力均**按HRC55计算的理论值。从上表也可看出当硬度低于HRC53时,即使留有1.2的安全系数,使用也不安全了,特别当硬度只有HRC50时,1.7倍的安全系数也形同虚设,非常危险。硬度不够较易造成回转支承失效,从滚道表面点蚀开始到坍塌结束。 *滚道淬硬层深度 滚道淬硬层深度目前尚无无损检测的方法,主要靠工艺和装备来保证,必要的淬硬层深度是回转支承滚道不产生剥落的保证。当回转支承受外负荷作用时,钢球与滚道的点接触就变成了面接触,是一个长半轴为a,短半轴为b的椭圆面,滚道除受压应力外,还受到剪切应力作用,较大剪切应力发生在表面下0.47a深处,因此滚道淬硬层深度须大于0.47a(一般取0.6a),这也是标准中根据钢球直径大小,而不是根据回转支承直径大小来规定淬硬层深度的原因,同时给出了具体较小保证值。深度不够又会对回转支承的承载能力产生什么样的影响呢?它定量化的描述是:额定静容量CO与淬硬层深度H0.908成正比,由此可计算出,将要求为4mm的淬硬层深度只淬到2.5mm,那么CO将由1降至0.65,由此而产生的回转支承失效形式为滚道剥落,即使采取焊补措施也无济于事。 *滚道曲率半径 这里的滚道曲率半径是指滚道在垂直剖面内的曲率半径,它与钢球半径的比值t(一般为1.04~1.08)的大小也显着影响着回转支承的额定静容量和动容量(寿命Lh),设t=1.04时为额定静容量和寿命均为1,则有下列对比关系: 从表中可看出半径比越大额定静容量越低,使用寿命越短,即使滚道热处理硬度和淬硬层深度都符合标准要求,而不能有效控制该半径比,回转支承的承载能力和使用寿命仍达不到标准值,而这一点往往被忽视,但它却是影响回转支承性能的重要参数。 滚道曲面是通过成型砂轮磨削得到的,砂轮的修整精度直接复印到滚道上,砂轮修正时主要有三个误差源:半径对刀误差,上、下圆弧偏心距误差和修正笔回转误差,其中**个误差的大小除与装备水平有关外,很大程度上取决于操作工的责任心和操作水平,因此有很大的不确定性,对刀误差影响着滚道半径,且它和偏心距误差共同影响着滚道接触角。 滚道接触角α 该接触角是指钢球在滚道上的接触点和钢球球心连线与回转支承径向剖面(水平面)之间的夹角。回转支承的额定静容量CO与sinα成线性正比,一般原始接触角α取45o,之所以称之谓原始接触角,是因它是滚道设计计算和测量的角度,在回转支承轴、径向间隙为0时,原始接触角和装配后的实际接触角一致,当回转支承有间隙时,实际接触角大于原始接触角,间隙越大,实际接触角越大,在标准规定的间隙范围内一般将增加2o~10o,即实际接触角将达到47o~55o,这是一个对承载能力有利的变化,如果原始接触角和间隙都较大,实际接触角**过60o,随着滚道的磨损间隙将进一步加大,实际接触角也将增大,也就是钢球的落点向滚道边缘靠近,这时将出现接触椭圆面**出滚道边缘,滚道实际受力将**理论计算应力,而造成滚道边缘压溃,回转支承失效。因此控制好原始接触角和装配间隙已不是一个简单的精度问题,而是保证承载能力和使用寿命的大事。 影响原始接触角的因素是滚道半径误差和上、下半弧偏心距的误差,而实际接触角以原始接触角为较小值,随着间隙的加大而加大,当钢球与滚道的曲率比不同时,同样的滚道半径和上、下弧偏心距误差对原始接触角误差大小的影响程度不同. 同样,装配间隙对实际接触角的影响也与曲率比有关,曲率比越小,实际接触角越大,换言之曲率比越小,原始接触角越难控制,间隙对实际接触角影响越大。轴向间隙对接触角的 从提高滚道的承载能力角度考虑,我们希望滚道与钢球的半径比越小越好,然从控制接触角角度考虑,又不希望太小。目前国内大多数回转支承厂普遍使用的砂轮修整方式都很难兼顾两者。顾此失彼,而这往往被一些制造厂有意无意地忽视了。不是接触角失控就是采用增大滚道半径牺牲滚道承载能力来控制接触角,不管哪种情况出现都是用户所不愿接受的。 解决这一矛盾的有效办法是采用数控装置修整砂轮。数控三坐标联动自动修整,从原理上避免了半径对刀和偏心距调整而产生的误差,滚道半径和原始接触角得到有效保证。如果我们把滚道的淬火硬度和淬硬层深度称之谓滚道的“硬件”,那么滚道的半径和接触角就是滚道的“软件”,只“硬”不“软”事倍功半,只有“软、硬”兼备的滚道才是回转支承品质的保证。数控三坐标联动修整砂轮,有效地保证了滚道的“软件”水平,而滚道在热处理之前的数控车削,则为“硬件”提供了重要保证,这种保证体现在两个方面,其一:数控车削的滚道曲面、形状规则、表面粗糙度低、滚道边口圆弧倒角半径一致,且与滚道面平滑连接。规则的滚道曲面,使淬硬层深度均匀成为可能,平滑连接的倒角避免了淬火时的“尖角效应”,根除了滚道边口易淬裂的缺陷。一致的倒角半径解决了过大的倒角造成的滚道有效承载区域的缩小,使钢球在滚道上的接触面过早地到达边口,而影响使用寿命。其二:数控车削的滚道曲面,除表面粗糙度外,其余尺寸与磨削后的滚道曲面完全一致,因此滚道的磨削量很小(为普通方法加工的1/2~1/3),较大限度地保留了淬硬层深度和表面硬度,同时数控车削滚道使内、外圈的滚道中心直径的一致性得到了很好的保证,避免了因配磨而损失的淬硬层深度和表面硬度,进一步提高了回转支承的承载能力和使用寿命。 综上所述,只有“软、硬”兼备的滚道,才是回转支承承载能力的有效保证,而数控化加工是目前较有效和较可靠的手段。 造成挖掘机用回转支承早期失效的主要原因有二条:一是断齿;二是滚道破坏。其中,断齿是主要原因,占90%以上,且绝大多数发生在挖掘机出厂后六个月以内。这不但严重困扰着回转支承制造厂产品质量信誉,同时也对主机厂产品市场造成不利影响,因此认真解决好这一问题是回转支承制造厂和主机厂的共同的目标和责任,也是双方进一步合作共同发展的根本保证。 因断齿而使回转支承早期失效的根本原因是什么呢?设计问题;制造问题,材质问题;装配问题还是使用问题。透过下列现象不难发现问题的本质之所在:①在过去的十二年里,马鞍山回转支承厂共为各类主机配套回转支承二万余套,除挖掘机行业外,仅有一起回转支承断齿记录,而且是发生在晚期。当然,挖掘机的工况较塔吊、汽车吊等其它大部分使用回转支承的行业的主机工况要恶劣,回转速度较快,冲击负荷也较大,断齿的可能性相应地也大些,这也是不争的事实。因此,挖掘机用回转支承的模数较同一滚道直径的其它行业主机用回转支承要大一档,而且是硬齿面(一般在47HRC~58HRC之间选取不同的硬度段),基本满足了挖掘机对回转支承齿轮的要求。虽然统计资料表明挖掘机用回转支承早期断齿的概率大于其它主机,但也**于较少的二、三种挖掘机上,大部分机种较少有回转支承早期断齿事故发生。②从我们掌握的资料分析,国内外绝大多数20~22吨级的挖掘机使用的回转支承齿轮模数都为10mm (或径节 =2.5),热处理和精度等级基本一致,国产挖掘机一般采用标准齿高和标准压力角。回转支承齿轮周向许用力P可按下式计算: P=Kz*m*b/78 (吨) 式中 Kz=(z/150)^(±0.09)外齿取+;内齿取- z-齿数m-模数mmb-齿宽mm 若设齿宽b=80;齿数z=90~110;且为内啮合,则齿轮周向许用力为: p=(90~110/150)^(-0.09)*10*80/78 =10.74~10.55(吨) 可见齿轮的周向许用力能够满足该吨级的挖掘机对回转支承齿轮负荷要求,但在该级别中个别机型出现的回转支承早期断齿率却高达2%,其它绝大部分机型无此现象发生。 ③通过对多起早期断齿实物的分析研究发现,大部分断齿发生在沿齿宽方向的上半部,一半以上的断裂面与轮齿的上端面相交,并成45°~60°左右的夹角,即使全齿脱落其裂纹也是自上而下扩张所致。齿轮受挤压而产生的塑性变形也相当明显,且上部较下部严重得多,整圈齿槽宽都有不同程度变化,从下至上、从根至**齿槽宽递增。 我们是否可以认为:造成挖掘机回转支承早期断齿的作用力并非是周向回转驱动力,而是与之啮合的小齿轮对其施加的径向挤压力,且挤压时小齿轮的轴线与回转支承齿轮轴线不平行。该力产生于挖掘过程中地面对斗的反作用力,由于回转支承有间隙的原故,与回转支承内外圈分别联接的上下两部分在倾覆力矩的作用下,将发生在回转支承通过大臂的轴向剖面上的相对倾斜,同时产生沿回转支承径向与大臂反方向的相对位移,位移量与回转支承径向间隙相当。因与回转支承啮合的小齿轮安装在大臂的相反方向,当两者齿侧间隙过小时,位移尚未完成,小齿轮便压上大齿轮,这种情况下本应由回转支承滚道承担的负荷却由齿轮担当了,由于小齿轮是悬臂安装原本倾斜的轴线在挤压力的反作用下进一步加剧,致使作用在大齿轮上的挤压力集中在齿宽的上部。开始齿轮由塑性变形来补偿齿侧间隙的不足,随着回转支承滚道的进一步磨合,其径向间隙渐渐加大,而变形量却是有限的。通过受力分析可以看到:小齿轮对大齿轮的挤压力是地面对斗的反作用力的几倍甚至十几倍,并且作用在齿廓上的力将被再一次放大,压力角越小放大系数越大。这一经过两次放大的力足以造成大小齿轮断齿。以上分析的结论与*③条现象是吻合的。 因此,笔者认为:回转支承早期断齿的根本原因是与小齿轮的配合侧隙过小。建议侧隙值不小于回转支承径向间隙的1.25倍。值得参改的是,我厂近期为加拿大制造的四种型号的挖掘机用回转支承的齿轮压力角分别为25°和27°,国内合资厂也有采用。这对提高齿轮抗径向挤压能力是有效的。 当然,诸如回转支承材质缺陷;齿淬后残余内应力较大、内部有裂纹;因回转支承滚道失效回转卡滞;挖掘机违章操作等也可导致回转支承齿轮早期失效,但应该分布面较广且离散。 一、单排球式回转支承的选型计算 1、计算额定静容量 C0 = f ·D·d 式中:Co --额定静容量,kN f--静容量系数,0.108 kN / mm2 D--滚道中心直径,mm d--钢球公称直径,mm 2、根据组合后的外载荷,计算当量轴向载荷 式中:Cp --当量轴向载荷,kN M--总倾覆力矩,kN·m Fa --总轴向力,kN Fr --总倾覆力矩作用平面的总径向力,kN 3、计算安全系数 fs = Co / Cp fs值可按下表选取。 二、三排柱式回转支承的选型计算 1、计算额定静容量 C0 = f ·D·d 式中:Co --额定静容量,kN f--静容量系数,0.172 kN / mm2 D--滚道中心直径,mm d--上排滚柱直径,mm 2、根据组合后的外载荷,计算当量轴向载荷 式中:Cp --当量轴向载荷,kN M--总倾覆力矩,kN·m Fa --总轴向力,kN 3、计算安全系数 fs = Co / Cp fs值可按下表选取。 回转支承安全系数fs