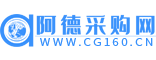
时间:2007-10-10 12:00:00 点击:211
由于微丸有着优越的性能,开发用工业方法制备大小均一、圆球度好、表面光洁的微丸有着巨大的应用前景。医药工业缓释、控释制剂的发展更迫切需要开发大规模制丸的设备。为了满足市场需求,公司在充分吸收国内外制丸先进技术基础上,较新研发出新一代微丸设备-挤出滚圆机系统,它能够以工业化大规模批量制造出球形微丸。制丸方法简单、效率高。本系统由挤出制条机和离心滚圆机组成,(关于挤出制条机和离心滚圆机在后面有详细的介绍),该系统不但可以作为医药缓释、控释制剂新品种研发的优良设备,还可作食品、化肥、催化剂、精细化工等行业需制丸的可以选择设备。 1 用挤出滚圆法制丸的特点 在各种制丸方法中,由挤出滚圆法制微丸,已成为目前国际上十分流行的一种制丸方法。它有如下几个特点: (1)生产能力大,设备费用较低; (2)微丸直径由挤出孔板决定,容易控制,造粒范围广,可以制造0.3~5 mm的球粒,颗粒的直径大小相同,分散带小; (3)造粒后球粒内的含量均匀; (4)颗粒形状可为球形、柱形及不定形;以球形较好,容易包衣; (5)可根据不同材料的性质,在物料较适合的条件下制丸。 由于药物控释、缓释制剂的发展,对球形微丸的要求骤增。药物释放系统的球粒不仅在**上有优点,例如:流动性能好,不易破碎,球粒的大小尺寸均匀,分布带窄,容易包衣和装填均匀,而且容易再现血药水平,在技术也有优点。 2 挤出滚圆法制微丸的设备 用挤出滚圆制造微丸的设备包括挤出制条机和离心滚圆机。 挤出制条机是使软材成型为长圆柱形挤出物的装置。我公司开发出的有螺杆式前挤出制条机和螺杆式侧挤出制条机两种。 离心滚圆机是使挤出机挤出的圆条均匀的切割成与直径相等的圆柱形小颗粒并滚制成微丸的设备。挤出的圆条在滚圆盘上被剪切成与圆柱直径大致相同的长度后,再经高速旋转的滚圆盘滚制成圆球状微丸,我公司设计出的*特齿盘边缘上具有对球丸进行抛光的功能。滚圆盘有许多特殊的破断齿构成,呈密集点状分布,这些破断齿通常高1-2mm,相距2-4mm不等。 3. 挤出滚圆法制微丸的过程 挤出滚圆制微丸一般经过以下5步才能制得合格的微丸: ① 干粉混合 一定粒径范围内的物料干粉(包括辅料或药物/辅料/中药浸膏等). ② 制软材 在干粉物料中以适宜速度加润湿剂,充分混和均匀,使之具有适度粘弹性和塑性。(以上过程可在湿法混合制粒机中完成). ③ 软材挤出 软材经挤出机挤出,挤出物在重力作用下呈弯曲条状或经切割断裂成不规则长度的短枝,且表面光滑(此过程在螺旋挤出机中完成)。 ④ 离心滚圆 挤出条移至离心滚圆机内,经滚圆机底盘上的齿将其剪切成与圆柱直径大致相同的长度后,再在高速旋转的滚圆盘上滚制成圆球状微丸。(此过程在离心滚圆机内完成)。 ⑤ 微丸干燥/包衣 滚圆后将微丸进行适度干燥,使其具有一定硬度、球形度和机械特性,同时控制微丸的水分含量,便于进一步加工和质量控制。该过程制得的微丸可继续进行包衣。(该过程可在流化床干燥包衣机中完成)。 4 影响微丸质量的因素 挤出速度、滚圆速度和滚圆时间等因素对微丸质量也有很大影响。 提高挤出速度可提高生产效率,但挤出速率越高,挤出物质量越差。适量加入高HLB值的表面活性剂,能够有效克服挤出物表面缺陷。 滚圆时间和滚圆速度均与处方组成、物料特性密切相关,应视具体情况确定较佳滚圆时间和速度。以中药为例,尽管多种中药原料粉体之间存在一些差别,但只要通过优化水分比例、滚圆速度和滚圆时间等关键工艺参数,一般都能获得令人满意的目标产品. 5. 载物量的因素 用挤出滚圆法制备微丸,若制备过程中水分比保持不变,随着载物量的增加,会逐步出现双粒、哑铃状颗粒、颗粒质量良好、大颗粒、结块等现象,颗粒粒径也随载物量的增加而增大。这是由于颗粒在滚圆盘上滚动时,受重力、圆盘支持力、筒壁支持力、圆盘和筒壁对颗粒的摩擦力及颗粒间的挤压力、摩擦力及粘合力等作用力的协同作用。若挤出物中水分比相同,则颗粒的塑性、强度和粘合力相同。颗粒在滚圆盘上一方面作螺旋起落运动,一方面作自转运动。当载物量增大时,靠近筒壁部位的颗粒所受挤压力较大;另外,颗粒间碰撞、挤压的机率也增大。当颗粒的塑性变形增加,从较圆的球形变成椭圆形或扁平状时,颗粒间的接触面积增大,摩擦力和粘合力变大,颗粒粘附在一起,形成较大颗粒;随着颗粒表面的干燥,颗粒间粘合力降低,颗粒形成更大颗粒的可能性减小,较终造成颗粒分布带较宽,粒径普遍较大的现象。当载物量进一步增大时,结块就更严重,并且由于这些结块颗粒的质量较大,处于转盘底部时,所受挤压力更大;同时受转盘摩擦力变大及转盘表面形状的影响,颗粒在转盘上间歇性跳跃,而跳跃过程中颗粒自转较慢或不自转,摩擦接触面固定,形成了圆整度较差的大颗粒,甚至不规则的粘结块。 在工业化生产中,为提高产量,滚圆机的载物量必须提高,这时可通过降低物料中水分来得到质量较好的颗粒。但是在实际生产中也并不能简单地依靠降低载物量增大时的水分比来控制颗粒的粒径。经我公司实验人员长期研究后得出,物料强度同周向压力有关。载物量增大,必然引起周向压力的增大,进而导致挤出强度的增加;挤出物破断长度增加,也会引起颗粒直径的增大。因此,对于载物量增加时颗粒粒径增大的原因,应作具体分析:是由于水分偏高引起小颗粒团聚造成的,还是由于水分偏低使挤出物破断长度增大造成的。这主要靠经验来判断,观察制得颗粒的外观质量,如其中是有双粒或哑铃状颗粒还是有少量粒径较大的圆颗粒出现。 6. 单(双)螺杆挤出机的特点及构造 前出料制粒机的特点: 1、 剖分式机筒,易于拆卸、清洗 2、 机筒设夹套,可进行冷却或加热 3、 多种出料孔板,有平板形孔板、半球形孔板等,适应多种物料 4、 大型设备有强制进料装置,生产效率高 5、 可配置切割刀,制取长短一致的颗粒 6、 挤出孔板可根据需要设置各种形状 侧挤出制粒机的特点: 1、连续作业,生产效率高。 2、挤压均匀,密度好,成品率高。 3、多种孔径的网孔板,可挤出0.5mm-3.0mm圆柱条状物。 4、与前挤出机相比,侧向挤出机的挤压过程物料受力小,产生的摩擦少,对挤出物塑性变形能力的增大起到了积极的作用。对热敏性物料可进行快速、无热挤压。 5、针对特殊物料的要求,挤出机可加装冷却或加热夹