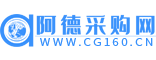
时间:2007-05-10 12:00:00 点击:99
一、TPM的定义(全公司的TPM) 全公司的TPM的定义有以下五个方面: 1、追求生产系统的效率化的极限(综合效率化),以提高企业的素 质为目标; 2、延长生产系统的生命周期,预防“灾害损耗、不良损耗、故障损耗”等一切损耗,并在现场落实具体措施; 3、涉及以生产部门为首的开发、经营、管理等一切部门; 4、从总经理到**工作人员全体人员参加; 5、通过重复的小集团活动,达到零损耗。 二、TPM的目标 TPM的目标是“通过改善人和设备的素质,来改善企业的素质。” 所谓人的素质就是要使全体员工都具有兢业的思想、不断改善的意识,同时具备岗位所要求的知识和技能。具体的来说,除了干劲和意识,作为操作人员应具备自主保养的能力;作为维修人员应具备保养机电一体化设备的能力;作为生产技术人员应具备设计出不需保养的设备的能力。 所谓设备的素质主要体现在两个方面,一是改善现有设备,提高综合效率。即以低的投入(人、设备、原材料)达到高的产出(产量、质量、成本、交货期、安全卫生、作业积极性)。随着自动化的不断推进,生产的主体越是从人的操作技能转向设备,因此消除影响设备效率的各种损耗,使设备更有效率的工作,也便成了TPM的目标。二是实现新设备的LCC(Life Cycle Cost)设计和垂直提高。即设备的设计要在考虑了设备的整个使用周期所需费用的基础上进行。垂直提高就是指新设备从运转一开始就立即进入稳定的工作状态。 三、设备的七大损耗? 要使设备达到较高效率,就要发挥设备所具备的功能和性能。反过来,如能彻底地去除阻碍效率的损耗,就能提高设备的效率。但是损耗的类型是以行业的不同而各不相同的,例如作为机械行业,大致可分为七种损耗: 1、故障损耗 故障可分为功能停止型故障和功能下降型故障两大类。无论是哪一类故障,故障损耗是阻碍效率化的较大原因。 2、准备、调整损耗 设备从生产**个产品,然后中止,到生产出下一个产品为止,这其中的准备、调整阶段的停机就是准备、调整损耗。其中主要的是“调整时间” 3、刀具调换损耗 因刀具寿命而调换刀具的时间,刀具折损引起的报废、修整时间,均称为刀具损耗。 4、加速损耗 加速损耗就是从开始生产时到生产稳定化时的时间。由于加工条件的不稳定性,夹具、模具的不完备,试切削损耗、作业人员的技术水平等因素,其 发生量不同。 5、检查停机损耗 所谓检查停机,与普通的故障不同,是指因暂时的小故障而停止设备或设备处于空转状态,如传感器因某种原因引起误动作,一旦使之复位,设备就正常工作,。 6、速度损耗 所谓速度损耗技术实际运行速度比设备的设计速度慢。 7、废品、修正损耗 即是因废品、修正引起的损耗。废品固然是损耗,次品由于要修正也得花费许多不必要的人力、物力,因此也是一项不可忽视的损耗。 以上是机械行业7大损耗是影响设备效率的主要因素,因此解决这些损耗是提高设备效率化的要点。 四、设备损耗的计算方法 通过对设备损耗的计算,就可以对设备的综合的效率有一个了解,同时还可以为消除损耗提供方向性指导。 1、设备的时间工作率: 时间工作率就是设备实际工作时间与负载时间(必须使设备工作的时间)的比率,计算公式如下: 负载时间-停止时间 时间工作率=-------------------------------×100% 负载时间 负载时间是指1天(或者1个月)的操作时间中减去生产计划上的暂停时间,计划保养上的暂停时间,以及日常管理上需要去除的时间后所剩余的时间。因此所谓的停止时间就是故障、准备、调整及调换刀具等的时间。 2、性能工作率: 性能工作率=速度工作率×净工作率×100% 其中速度工作率就是设备实际的工作速度相对其固有能力而言的速度的比率要是速度工作率下降就可知设备速度下降损耗的程度。 基准周期时间 速度工作率=---------------------- ×100% 实际周期时间 净工作率表示设备是否在单位时间内按一定的速度工作,它并不是说比基准速度快了还是慢了,而是指即使在较慢的速度情况下是否是长时间地按这一速度稳定的工作。通过净工作率的计算,可以反映出检查停机等小故障产生的损耗。 加工数量(产量)× 实际周期时间 净工作率=--------------------------------------------------------×100% 负载时间-停止时间 设备的综合效率=时间工作率×性能工作率×正品率×100% 例:一天的负载时间为460分,工作时间为20分,准备时间为20分,调整时间为20分,基准周期时间为0.5/个,实际周期时间为0.8/个,一天的产量是400个,其中有8个废品,请计算出设备的综合效率。 解: 设备综合效率 =时间工作率×性能工作率×正品率×100% =0.87×0.5×0.98×100% ≈42.6% 五、开展TPM的8大支柱 要达到TPM的目的,必须开展以下8项活动,这称为“开展TPM的8大支柱” 1、个别改善 为追求设备效率化的极限,较大程度的发挥出设备的性能和机能,就要消除影响设备效率化的损耗,我们把消除引起设备的综合效率下降的七大损耗的具体活动叫个别改善。 2、自主保养体制的形成 “自己的设备自己保养”,所以自主保养活动是以运转部门为中心,以七个步骤展开。自主保养的中心是防止设备的劣化。只有运转部门承担了“防止劣化的活动”,保养部门才能发挥出其所承担的专职保养手段的真正威力,使设备得到真正有效的保养。 3、保养部门的计划保养体制的形成 在运转部门自主保养的基础上,设备的保养部门就能够有计划的对设备的劣化进行复原以及设备的改善保养。 4、运转保养的技能教育训练 不论是运转还是保养部门,仅有良好的愿望还难以把事情做好,因此我们必须加强技能的训练和提高。这里有一点需要说明的是,培训和教育训练不仅是培训部门的事,也是每个部门的职责,并且应成为每个职工的自觉行动。再则,随着社会的发展和进步,工作和学习已经不可分割地联系在了一起,学习和培训是工作的新的形式,我们要把学习融入到工作当中去,在工作中学习,在学习中工作。 5、设备初期管理体制的形成 为了适应生产的发展,必定有新设备的不断投入,于是我们要形成一种机制能按少维修、免维修思想设计出符合生产要求的设备,按性能、价格、工艺等要求对设备进行较优化规划、布置,并使设备的操作和维修人员具有和新设备相适应的能力,总之,要使新设备一投入使用就达到较佳状态。 6、品质保养体制的形成 为了保持产品的所有品质特性处于较佳状态,我们要对与质量有关的人员、设备、材料、方法、信息等要因进行管理、对废品、次品和质量缺陷的发生防范于未然,从结果管理变为要因管理,使产品的生产处于良好的受控状态。 7、管理间接部门的效率化体制的形成 管理间接部门的效率化主要体现在两个方面,这就是要有力地支持生产部门开展TPM及其他的生产活动,同时应不断有效地提高本部门的工作效率和工作成果。 8、安全、环境等管理体制的形成 “安全**”这是一贯的认识,但仅有意识是不够的,它必须要有一套有效的管理体制才能确保。 对卫生、环境也一样,我们要在不断提高意识的同时,要建立起一种机制来确保卫生、环境的不断改善。在目前来说,建立和实施ISO14000环境管理体系不失为一良策,一方面保护环境是我们对社会应尽的责任,同时也可以提高我们的企业形象。