西安匠恒机械模具有限公司
联系人:刘先生
电话:18629666389
地址:三桥蔺高工业园
产品规格:
产品数量:
包装说明:
关 键 词:塑料数控厂
行 业:加工 模具加工
发布时间:2022-09-26
数控编程
数控加工程序编制方法有手工(人工)编程和自动编程之分。手工编程,程序的全部内容是由人工按数控系统所规定的指令格式编写的。自动编程即计算机编程,可分为以语言和绘画为基础的自动编程方法。但是,无论是采用何种自动编程方法,都需要有相应配套的硬件和软件。
可见,实现数控加工编程是关键。但光有编程是不行的,数控加工还包括编程前必须要做的一系列准备工作及编程后的善后处理工作。一般来说数控加工工艺主要包括的内容如下:
⑴ 选择并确定进行数控加工的零件及内容;
⑵ 对零件图纸进行数控加工的工艺分析;
⑶数控加工的工艺设计;
⑷ 对零件图纸的数学处理;
⑸ 编写加工程序单;
⑹ 按程序单制作控制介质;
⑺程序的校验与修改;
⑻ 首件试加工与现场问题处理;
⑼数控加工工艺文件的定型与归档。
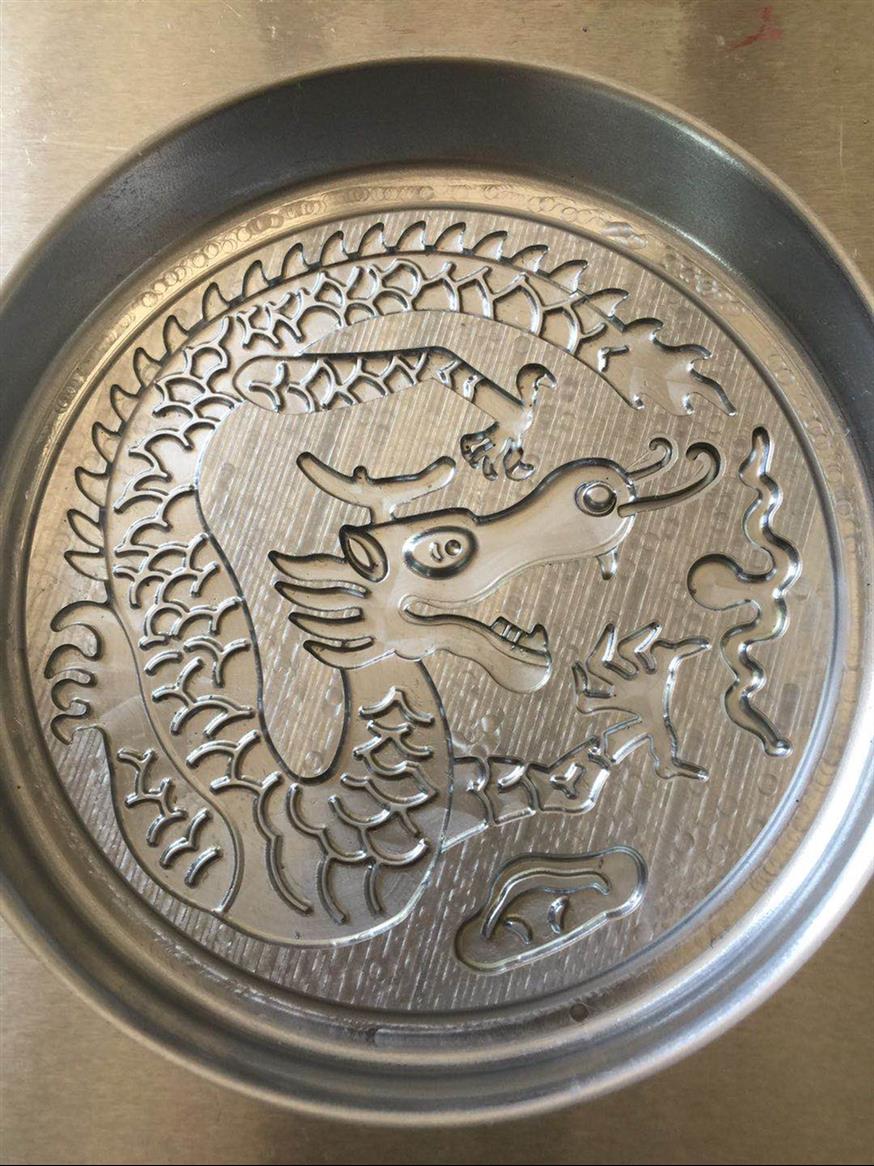
高速、、高精度、高可靠性
要提高加工效率,先必须提高切削和进给速度,同时,还要缩短加工时间;要确保加工质量,必须提高机床部件运动轨迹的精度,而可靠性则是上述目标的基本保证。为此,必须要有高性能的数控装置作保证。
●高速、
机床向高速化方向发展,可充分发挥现代材料的性能,不但可大幅度提高加工效率、降低加工成本,而且还可提高零件的表面加工质量和精度。速加工技术对制造业实现、、低成本生产有广泛的适用性。
新一代数控机床(含加工中心)只有通过高速化大幅度缩短切削工时才可能进一步提高其生产率。速加工特别是速铣削与新一代高速数控机床特别是高速加工中心的开发应用紧密相关。90年代以来,欧、美、日各国争相开发应用新一代高速数控机床,加快机床高速化发展步伐。高速主轴单元(电主轴,转速15000-100000r/min)、高速且高加/减速度的进给运动部件(快移速度60~120m/min,切削进给速度高达60m/min)、高性能数控和伺服系统以及数控工具系统都出现了新的突破,达到了新的技术水平。随着速切削机理、超硬耐磨**命材料和磨料磨具,大功率高速电主轴、高加/减速度直线电机驱动进给部件以及高性能控制系统(含系统)和防护装置等一系列技术领域中关键技术的解决,应不失时机地开发应用新一代高速数控机床。
依靠快速、准确的数字量传递技术对高性能的机床执行部件进行高精密度、高响应速度的实时处理,由于采用了新型,车削和铣削的切削速度已达到5000米~8000米/分以上;主轴转数在30000转/分(有的高达10万转/分)以上;工作台的移动速度:(进给速度),在分辨率为1微米时,在100米/分(有的到200米/分)以上,在分辨率为0.1微米时,在24米/分以上;自动换刀速度在1秒以内;小线段插补进给速度达到12米/分。根据率、大批量生产需求和电子驱动技术的飞速发展,高速直线电机的推广应用,开发出一批高速、的高速响应的数控机床以满足汽车、农机等行业的需求。还由于新产品更新换代周期加快,模具、航空、等工业的加工零件不但复杂而且品种增多。
●高精度
从精密加工发展到**精密加工(特高精度加工),是世界各工业强国致力发展的方向。其精度从微米级到亚微米级,乃至纳米级(<10nm),其应用范围日趋广泛。**精密加工主要包括**精密切削(车、铣)、**精密磨削、**精密研磨抛光以及**精密特种加工(三束加工及微细电火花加工、微细电解加工和各种复合加工等)。随着现代科学技术的发展,对**精密加工技术不断提出了新的要求。新材料及新零件的出现,更高精度要求的提出等都需要**精密加工工艺,发展新型**精密加工机床,完善现代**精密加工技术,以适应现代科技的发展。

选择数控铣削用
在数控加工中,铣削平面零件内外轮廓及铣削平面常用平底立铣刀,该有关参数的经验数据如下:一是铣刀半径RD 应小于零件内轮廓面的小曲率半径Rmin,一般取RD=(0.8一 0.9)Rmin。二是零件的加工高度H< (1/4-1/6)RD,以保证有足够的刚度。三是用平底立铣刀铣削内槽底部时,由于槽底两次走刀需要搭接,而底刃起作用的半径Re=R-r,即直径为 d=2Re=2(R-r),编程时取半径为Re=0.95 (Rr)。对于一些立体型面和变斜角轮廓外形的加工,常用球形铣刀、环形铣刀、鼓形铣刀、锥形铣刀和盘铣刀。
数控机床上大多使用系列化、标准化,对可转位机夹外圆车刀、端面车刀等的刀柄和刀头都有标准及系列化型号对于加工中心及有自动换刀装置的机床,的刀柄都已有系列化和标准化的规定,如锥柄系统的标准代号为TSG-JT,直柄系统的标准代号为DSG-JZ,此外,对所选择的,在使用前都需对尺寸进行严格的测量以获得数据,并由操作者将这些数据输入数据系统,经程序调用而完成加工过程,从而加工出合格的工件。
刀点
究竟从什么位置开始移动到的位置呢?所以在程序执行的一开始,必须确定在工件坐标系下开始运动的位置,这一位置即为程序执行时相对于工件运动的起点,所以称程序起始点或起刀点。此起始点一般通过对刀来确定,所以,该点又称对刀点。在编制程序时,要正确选择对刀点的位置。对刀点设置原则是:便于数值处理和简化程序编制。易于找正并在加工过程中便于检查;引起的加工误差小。对刀点可以设置在加工零件上,也可以设置在夹具上或机床上,为了提高零件的加工精度,对刀点应尽量设置在零件的设计基准或工艺基谁上。实际操作机床时,可通过手工对刀操作把的刀位点放到对刀点上,即“刀位点”与“对刀点”的重合。所谓 “刀位点”是指的定位基准点,车刀的刀位点为刀尖或刀尖圆弧中心。平底立铣刀是轴线与底面的交点;球头铣刀是球头的球心,钻头是钻尖等。用手动对刀操作,对刀精度较低,且效率低。而有些工厂采用光学对刀镜、对刀仪、自动对刀装置等,以减少对刀时间,提高对刀精度。加工过程中需要换刀时,应规定换刀点。所谓“换刀点”是指刀架转动换刀时的位置,换刀点应设在工件或夹具的外部,以换刀时不碰工件及其它部件为准。
切削用量
数控编程时,编程人员必须确定每道工序的切削用量,并以指令的形式写人程序中。切削用量包括主轴转速、背吃刀量及进给速度等。对于不同的加工方法,需要选用不同的切削用量。切削用量的选择原则是:保证零件加工精度和表面粗糙度,充分发挥切削性能,保证合理的耐用度,并充分发挥机床的性能,大限度提高生产率,降低成本。
1、确定主轴转速
主轴转速应根据允许的切削速度和工件(或)直径来选择。其计算公式为:n=1000 v/7 1D式中: v?切削速度,单位为m/m动,由的耐用度决定; n一一主轴转速,单位为 r/min,D为工件直径或直径,单位为mm。计算的主轴转速n,后要选取机床有的或较接近的转速。
2、确定进给速度
进给速度是数控机床切削用量中的重要参数,主要根据零件的加工精度和表面粗糙度要求以及、工件的材料性质选取。大进给速度受机床刚度和进给系统的性能限制。确定进给速度的原则:当工件的质量要求能够得到保证时,为提高生产效率,可选择较高的进给速度。一般在100一200mm/min范围内选取;在切断、加工深孔或用高速钢加工时,宜选择较低的进给速度,一般在20一50mm/min范围内选取;当加工精度,表面粗糙度要求高时,进给速度应选小些,一般在20--50mm/min 范围内选取;空行程时,特别是远距离“回零”时,可以设定该机床数控系统设定的高进给速度。
3、确定背吃刀量
背吃刀量根据机床、工件和的刚度来决定,在刚度允许的条件下,应尽可能使背吃刀量等于工件的加工余量,这样可以减少走刀次数,提高生产效率。为了保证加工表面质量,可留少量精加工余量,一般0.2一0.5m m,总之,切削用量的具体数值应根据机床性能、相关的手册并结合实际经验用类比方法确定。
同时,使主轴转速、切削深度及进给速度三者能相互适应,以形成佳切削用量。
切削用量不仅是在机床调整前必须确定的重要参数,而且其数值合理与否对加工质量、加工效率、生产成本等有着非常重要的影响。所谓“合理的”切削用量是指充分利用切削性能和机床动力性能(功率、扭矩),在的前提下,获得高的生产率和低的加工成本的切削用量。
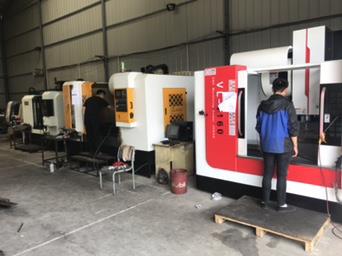
上道工序的加工不能影响下道工序的定位与夹紧 [2] 。
⑵先内后外,即行内部型腔(内孔)的加工,后进行外形的加工。
⑶以相同的安装或使用同一把加工的工序,好连续进行,以减少重新定位或换刀所引起的误荠.
⑷在同一次安装中,应行对工件刚性影响较小的工序。
加工路线
数控车床进给加工路线指车刀从对刀点(或机床固定原点)开始运动起,直至返回该点并结束加工程序所经过的路径,包括切削加工的路径及切人、切出等非切削空行程路径。
精加工的进给路线基本上都是沿其零件轮廓顺序进行的,因此,确定进给路线的工作是确定粗加工及空行程的进给路线。
在数控车床加工中,加工路线的确定一般要遵循以下几方面原则。
①应能保证被加工工件的精度和表面粗糙度。
②使加工路线短,减少空行程时间,提高加工效率。
③尽量简化数值计算的工作量,简化加工程序。
④对于某些重复使用的程序,应使用子程序。
使加工程序具有短的进给路线,不仅可以节省整个加工过程的执行时间,还能减少一些不必要的消耗及机床进给机构滑动部件的磨损等。短进给路线的类型及实现方法如下。
⑴短的切削进给路线。切削进给路线短,可有效提高生产效率,降低损耗。安排短切削进给路线时,还要保证工件的刚性和加工工艺性等要求。
⑵短的空行程路线。
①巧用起刀点。采用矩形循环方式进行粗车的一般情况示例。其对刀点A的设定是考虑到精车等加工过程中需方便地换刀,故设置在离毛坯件较远的位置处,同时,将起刀点与其对刀点重合在一起
②巧设换刀点。为了考虑换刀的方便和,有时将换刀点也设置在离毛坯件较远的
位置处,那么,当换*二把刀后,进行精车时的空行程路线必然也较长;如果将*二把刀的换刀点也设置在中的毋点位置上,则可缩短空行程距离。
③合理安排“回零”路线。在手工编制复杂轮廓的加工程序时,为简化计算过程,便于校核,程序编制者有时将每一刀加工完后的终点,通过执行“回零”操作指令,使其全部返回到对刀点位置,然后再执行后续程序。这样会增加进给路线的距离,降低生产效率。因此,在合理安排“回零”路线时,应使**刀的终点与后一刀的起点间的距离尽量短.或者为零,以满足进给路线短的要求。另外,在选择返回对刀点指令时,在不发生干涉的前提下,尽可能采用x、z轴双向同时“回零”指令,该功能“回零”路线是短的。
⑶大余量毛坯的阶梯切削进给路线。列出了两种太余量毛坯的切削进
给路线。是错误的阶梯切削路线,按1斗5的顺序切削,每次切削所留余量相等,是正确的阶梯切削进给路线。因为在同样的背吃刀量下。
⑷零件轮廓精加工的连续切削进给路线。零件轮廓的精加工可以安排一刀或几刀精加工工序.其完工轮廓应由后一刀连续加工而成,此时,的进、退位置要选择适当,尽量不要在连续的轮廓中安排切人和切出或换刀及停顿,以免因切削力突然变化而破坏工艺系统的平衡状态.致使零件轮廓上产生划伤、形状突变或滞留刀痕。
⑸的进给路线。在数控车削加工中,一般情况下。的纵向进给是沿着坐标的负方向进给的,但有时按其常规的负方向安排进给路线并不合理。甚至可能损坏工件。
优缺点
数控加工有下列优点:①大量减少工装数量,加工形状复杂的零件不需要复杂的工装。如要改变零件的形状和尺寸,只需要修改零件加工程序,适用于新产品研制和改型。②加工质量稳定,加工精度高,重复精度高,适应*行器的加工要求。③多品种、小批量生产情况下生产效率较高,能减少生产准备、机床调整和工序检验的时间,而且由于使用佳切削量而减少了切削时间。④可加工常规方法难于加工的复杂型面,甚至能加工一些无法观测的加工部位。数控加工的缺点是机床设备费用昂贵,要求维修人员具有较高水平。