在线分析监测系统的目的主要有三种:1安全,监测**标后会引起爆炸危险的介质,测量结果要参与联锁控制,确保人员和设备的安全。2过程控制,监测工艺生产状态是否正常,从而保证终产品质量。3环保监测,监测向环境排放的废气中对大气可造成污染的组分是否**标,控制生产过程对大气环境的污染。
对石化化工生产过程有着深刻的理解,可为广大石化化工用户提供全面的在线分析解决方案。
计算机诊断技术分析
CS3000属于DCS产品,适应于大型或中型化工过程控制,而HIS为CS3000系统操作站,基于Windows操作系统,对系统进行实时与过程操作。在CS3000系统中,一旦自动控制系统发生故障,便会及时发出告警信息,并详细记录,从而为查询故障点,有效解决故障奠定坚实的技术数据支持。在CS3000系统中,告警主要划分为三种,即过程告警、系统告警、操作。不同类型告警都具备相应的显示窗口,在化工仪表控制系统出现故障的时候,仪表维护人员便可基于HIS所提供的告警提示信息评估故障,并及时采取有效措施快速准确消除故障,迅速恢复系统运行,从而提高化工仪表维护效率与水平,确保化工生产运行稳定性与安全性。

催化机理
热力学计算表明,低温、高压对合成氨反应是有利的,但无催化剂时,反应的活化能很高,反应几乎不发生。当采用铁催化剂时,由于改变了反应历程,降低了反应的活化能,使反应以显著的速率进行。合成氨反应的机理,先是氮分子在铁催化剂表面上进行化学吸附,使氮原子间的化学键减弱。接着是化学吸附的氢原子不断地跟表面上的氮分子作用,在催化剂表面上逐步生成—NH、—NH2和NH3,氨分子在表面上脱吸而生成气态的氨。
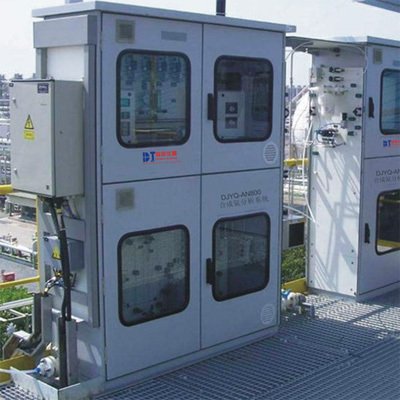
发现过程
合成氨合成塔
德国化学家哈伯(F.Haber,1868-1934)从1902年开始研究由氮气和氢气直接合成氨。 [2] 于1908年申请,即“循环法”,在此基础上,他继续研究,于1909年改进了合成,氨的含量达到6上。这是工业普遍采用的直接合成法。反应过程中为解决氢气和氮气合成转化率低的问题,将氨产品从合成反应后的气体中分离出来,未反应气和新鲜氢氮气混合重新参与合成反应。
合成氨反应式如下:(该反应为可逆反应,等号上反应条件为:“高温高压”,下为:“催化剂”)
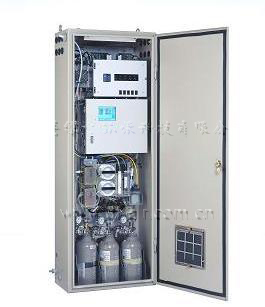
原料组成
合成氨的主要初始原料可分为固体原料、液体原料和气体原料。如天然气、石脑油、重质油和煤(或焦炭)等。 [3]
①天然气制氨。天然气先经脱硫,然后通过二次转化,再分别经过一氧化碳变换、二氧化碳脱除等工序,得到的氮氢混合气,其中尚含有一氧化碳和二氧化碳约0.10.3体积),经甲烷化作用除去后,制得氢氮摩尔比为3的纯净气,经压缩机压缩而进入氨合成回路,制得产品氨。以石脑油为原料的合成氨生产流程与此流程相似。
②重质油制氨。重质油包括各种深度加工所得的渣油,可用部分氧化法制得合成氨原料气,生产过程比天然气蒸气转化法简单,但需要有空气分离装置。空气分离装置制得的氧用于重质油气化,氮作为氨合成原料外,液态氮还用作脱除一氧化碳、甲烷及氩的洗涤剂。
③煤(焦炭)制氨。随着石油化工和天然气化工的发展,以煤(焦炭)为原料制取氨的方式在世界上已很少采用。中国能源结构上存在多煤缺油少气的特点,煤炭成为主要的合成氨原料,天然气制氨工艺则受到严格限制。