兰州100000级 GMP净化工程净化工程 安装
价格:0.00起
产品规格:
产品数量:
包装说明:
关 键 词:GMP净化工程净化工程
行 业:环保 净化工程
发布时间:2022-01-28
中净环球净化可提供GMP车间、GMP净化车间、GMP无菌车间的咨询、规划、设计、施工、装修改造等配套服务。
单向流工作室是一个“成套”的暖通空调系统,由空调系统、侧墙、吊顶空间及低速低位回风(工作室内前侧)等共同组成,该装置的设计意图是在处理危险物品时,为操作人员提供保护。送风HEPA过滤器(一般为安全更换型装置)可以安装在风管系统内,从风机到天花板静压空间,天花板应采用适当的材料,确保空气的均匀垂直层流,或者工作室的天花板直接由HEPA过滤器组成,由于采用了高压降的材料,因此系统就产生了从天花板垂直向下的均匀高速流。较高的换气率意味着,来自风机的热量将积聚在工作室内,因此系统一般需要安装冷却盘管,以保持工作室内的温度。
成品的储存温度和相对湿度根据产品参数、药典规定和其他资料确定,中国药典对药品的储存温度分为“阴凉处”、“凉暗处”、“冷处”和“常温”等四种情况,具体的储存温度分别是:阴凉处:<20℃;凉暗处:避光且<20℃;冷处:2~8℃;常温:10~30℃。药用包装材料的储存需要合适的温湿度条件,如硬壳,为防止其因温湿度过高而软化粘联、温湿度过低而硬化断裂,要求其储存的温度范围在 15~25℃,湿度范围在35~65%之间;从节能角度考虑,可在仓库内单辟一个储存间并配备相应的立空调系统;仓库应有“温度分布图”,以识别通常的“高温”和“低温”位置,并确定这些位置与室内传感器测量温度之间的关系。
企业应确定需要进行的确认或验证工作,以有关操作的关键要素能得到有效控制,确认或验证的范围和程度应经过风险评估来确定;企业的厂房、设施、设备和检验仪器应经过确认或验证,应采用经过验证的生产工艺、操作规程和检验方法进行生产、操作和检验,并保持持续的验证状态。设计确认主要依据的是生产质量管理规范(GMP)和根据产品特性所确定的用户需求(URS),确认一系列影响产品质量的环境参数,如温度、湿度、洁净等级、压差、气流流向等是合乎产品要求,设计确认可根据设计过程分阶段进行,由于HVAC系统的复杂性,在系统设备、风管等制作安装之前完成设计确认并预先发现问题加以解决,可有效避免施工过程中因变更造成的返工和时间损失,从而有效的控制了变更成本。基础设计阶段的设计确认审查要点:空调系统关键参数(温度、湿度、洁净级别、压差及流向);系统换气次数;系统空气过滤器选择;产品暴露/交叉污染控制;空调机组分区;循环风/直流风系统;系统监测和控制方案;排风过滤器;设备/过滤器规格和维修。详细设计阶段的设计确认审查要点,除了基础设计阶段审查要点外,还需考虑更多的因数,包括:室外空调参数;室外较端空调参数及其持续时间;空调系统新风和排风口位置;空调系统监测传感器数量和位置;空调系统报警策略;单个空调系统失效对生产的影响;回风利用及交叉污染控制;排风过滤器及其更换策略;室内送风/回风/排风口位置;加湿蒸汽质量;风管材料及风管系统泄漏率;空调设备/过滤器检修可操作性;室外设备维护/更换可操作性;系统工作寿命。
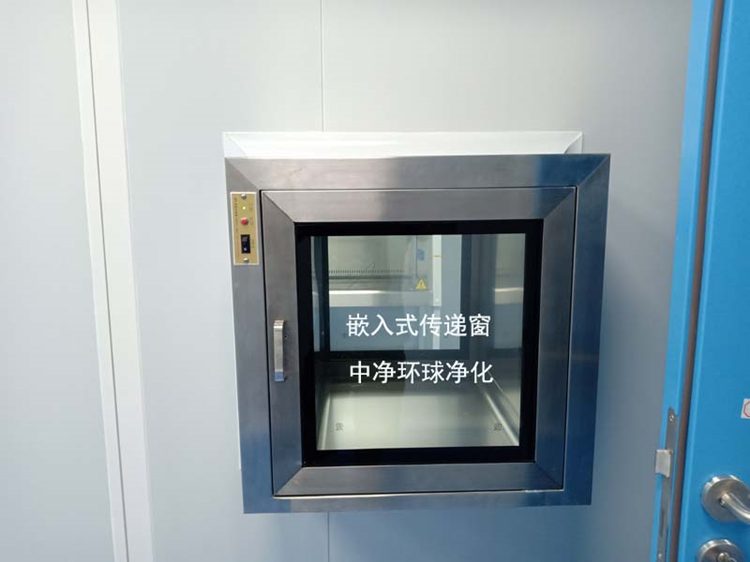
中净环球净化可提供GMP无尘车间、GMP洁净车间的咨询、规划、设计、施工、装修改造等配套服务。
制剂生产工艺简介
目前市场上销售的单克隆抗体药物绝大多数以剂的形式进行生产、销售和使用。
(1) 原液解冻
利用原液解冻装置(如水浴锅)将原液进行解冻,设置解冻温度和解冻时间,待完全解冻后进行配制和灌装。
(2)缓冲液配制
配制(可备料)相关的洁净区级别应根据产品的生产工艺确定。物料准备中应确保料量符合指令要求,标识清晰,应采用双人复核,避免投料量或转运过程中差错。使用自动称量系统的设备,应考虑称量系统的连接电缆、软管对称量线性和称量范围的准确性的影响。配液结束后对溶液的品质应进行必要的,如含量、pH等。除菌过滤可以降低灌装前的药液微生物的污染水平。过滤器与产品成分的相容性应在差条件下得到确认,通常使用两只过滤器串联过滤。推荐配液后直接过滤至缓冲罐,以缩短除菌过滤前的药液存放时间。药液配制过程中风险主要源自上一批次产品的残留污染。配制容器和附属系统先应考虑在线清洁和在线灭菌;必要时也可以考虑人工清洁、湿热灭菌后组装或组装后在线灭菌。
过滤后的滤器完整性应该进行检查,必要时过滤前滤器的完整性也应进行检查。完整性检查宜考虑在线检查。使用容易产尘的物料时应采取物理隔离、除尘或其他装置,降低污染。现场通风设施应能阻止气流引起的交叉污染。
(3)灭菌
制剂工序使用的铝盖、胶塞、西林瓶和器具都要经过灭菌的处理,应结合灭菌物的特性、要求(如除热原)选择合适的灭菌工艺。灭菌设备性能、灭菌工艺应得到验证。单克隆抗体产品因对热不稳定, 为非终灭菌产品,应采用无菌生产工艺(除菌过滤法或无菌操作法)进行制备。
(4)灌装
液体装量控制一般使用计量活塞泵或者时间-压力控制系统,装量更准确。通过活塞孔容积和螺杆间隙体积进行定量灌装、对无菌生产丁艺而言,灌装(或分装)是高风险的生产工序,除菌过滤后的药液、无菌原料药将直接暴露在开放空气条件下,虽然在A级环境下操作,但仍应该缩短灌装和密封(如扣塞)的时间以程度降低污染的可能。低温存放的产品应控制在低湿度条件下,以防止设备和容器的结露。灌装后部分产品(如对氧气敏感的粉针剂)需要通人除菌过滤的氮气,降低灌装中氧气的混入量。灭菌后灌装零部件应采取防止污染措施,如在A级保护或者密闭条件下传送。
(5)轧盖
轮盖工序主要是防止胶塞脱落,为产品提供长期的密封保证。轧盖区域应结合产品的密封性能、设备状况、铝盖特性等设计合适的洁净级别。轧盖过程中容易产生金属微粒或胶塞脱落现象,因此应考虑设定必要的除污染设施和检查装置,以消除污染和确保产品的密封完整性。
(6)灯检
通过灯检剔除个别有异物的产品,应通过生产工艺及其控制保证产品中产生异物的概率。灯检仅为防止有异物产品上市的措施。灯检人员的素质和培训水平、灯检台的照度和背景、灯检的时间是该工序效果的主要影响因素。采用自动灯检设备必须通过验证,不低于人工灯检的质量保证水平。相关的 SOP包括:灯检区的清场,灯检废品的管理,灯检设备的维护,灯检人吊的培训方法,灯检连续工作的时间规定等。
(7)包装
产品经贴标签、装箱后成为成品。包装线重要的是防止混淆。应确保标签正确,批号、生产日期和有效期等信息准确。产品数、标签消耗数等应合理平衡。为防止混绢,包装区应能防止无关人员进入。应有SOP规定防止标签信息差错、混淆的措施,数额平衡的检查方法和可接受标准等。
不同单克隆抗体药物其生产的工艺虽不同,但均可分为原液生产工艺和制剂生产工艺两部分。原液生产工艺主要包括:细胞培养工艺和纯化工艺两部分。目前在**的单克隆抗体市场,全人源化单克隆抗体是未来的发展方向。在FDA 批准上市的80多种基因工程和抗体工程产品中,抗体类产品有26种,其中18种为人源化抗体。
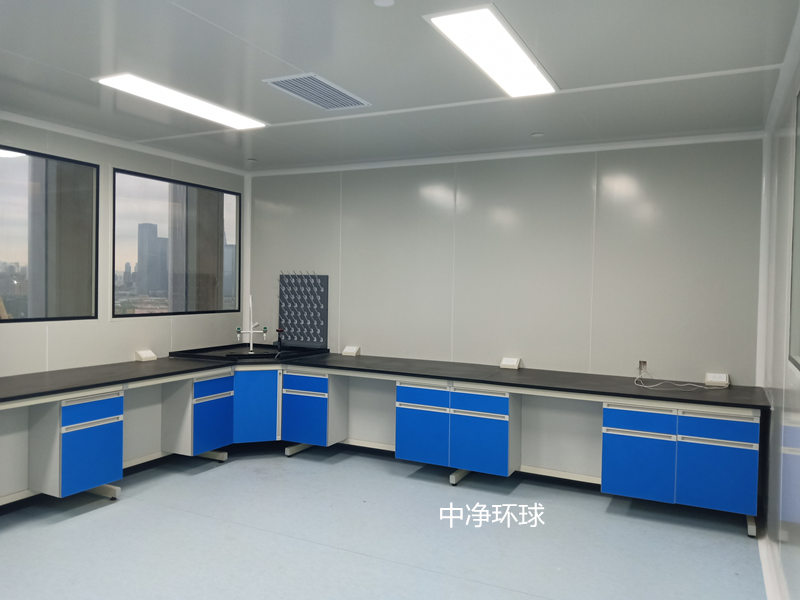
中净环球净化可提供GMP车间、器械GMP车间、诊断试剂GMP车间等洁净车间的咨询、规划、设计、施工、装修改造等配套服务,技术、经验丰富、价格实惠。
通风管道应符合《采暖通风与空气调节设计规范》,空气送风管道和一般的回风管道应采用镀锌钢制成,如果需要防腐或保持清洁(例如在洁净室内),则应采用不锈钢材质,不可采用能够增加微粒或易于滋生的内部保温材料,通风管道应设置适当的支架,以承载其自身重量和保温材料及管路中的设备和控制装置;如果噪声较大,可在HEPA过滤器前安装管道,如果振动较大,可考虑采用挠性支架和接头;若需采用挠性管道将支管连接到终端空气设备,应尽可能缩短其长度,不能**过3m。通风管道规格和方向变化较大,会噪声、振动和压降;从风机和空气处理机引出的管道应尽可能采用直管,若需在靠近风机处采用弯管,则须避免其引起使系统性能降低和功耗的“系统效应”。
为了减少空气泄漏,并避免将来发生较大的泄漏,应按照《通风与空调工程施工质量验收规范》相应的要求对通风管道进行密封,各个场所、空气系统和供应区域的管道泄漏百分率会有所不同;一般情况下,通风管道泄漏率不能**过1%(对于正压排气管和输送危险物质的正压管道,泄漏率应为 0%),应精心选择密封管道密封胶,确保其能够长期附着在镀锌钢材上,溶剂型密封胶和油基密封胶较难使用,且可能受到环境限制,但通常具有较长的寿命。风阀用于改变暖通空调系统内空气流动的方向、停止空气流动或改变空气流量;风门叶片可平行运动,也可相对运动;平行叶片风门转动方向相同,在从全开到全闭的行程中,相互间保持平行,相对叶片风门工作时,邻近的叶片转动方向相反;建议采用对开调节风阀,因其节流平稳,具有较好的线性特性(因为湍流较少);可采用较复杂的设计,以提高控制性能,但会增加成本。风阀应采用耐腐蚀材料制成,例如铝或 304 不锈钢;风阀中间轴应延伸到空气处理机组壳体外部,以便于安装执行机构。
GMP车间常用的气流组织的送风方式有三种:侧送、孔板送风、散流器送风,这些送风装置对于各房间/空间内外的空气分配至关重要;必须安装在正确的位置,才能保证空气在空间供气侧到回流侧的妥善分配和清扫作用,达到净化空气和清除污染物的均匀气流型式;安装位置不正确可能导致死区(局部微粒浓度)或气流过大(产生不利的空气湍流);对于空气需求量较少的分级空间,采用低流量多口通常比高流量单口效果好。终端过滤组件(过滤箱)采用从房间一侧可接近的 HEPA 过滤器,用于供给清洁空气,并防止空气处理机组未运转时污染空气从房间流出。
控制污染物浓度的方法有三种:稀释通风、工艺过程封闭;局部排气罩的设计对于达到与微粒的粒径和扩散方式相适应的捕集速度至关重要,该设计还应保证合理的噪声级和排气量。通风管道设计应基于恒定流速,确保微粒保持悬浮状态,防止其在管道中积聚;考虑到固体碰撞会引起腐蚀,管道厚度应足够大,且应平滑过渡,尽量减少弯管数量,以降低能耗、腐蚀和粉尘沉积的可能性,检修门便于进行日常检查和清洁;系统可设计为连续工作,以降低暖通空调系统关闭时设施内气体交叉流动导致污染的风险,在暖通空调系统平衡过程中,应考虑空气排放量;如果主集尘器利用逆流压缩空气自动清洁,设计和调试应考虑系统管道内流量周期性减小的影响。

中净环球净化可供GMP净化车间、GMP实验室、GMP无菌室的咨询、规划、设计、施工、装修改造等配套服务。
空气中含尘浓度和微生物量是无菌产品特别是某些生物制剂API洁净室环境条件的重要衡量标准,洁净室等级就是根据这些不同衡量标准的数值确定的。环境等级有几种类似的提法:ISPE 指南采用的是 ISO 标准的“级”,如“7 级”即为ISO7(每立方米 352000 个微粒—动态,0.5μm 粒径),微生物限值为 10cfu/m3 。通过对比,ISPE 的“7 级”同欧洲标准的B级很相似,不同的是欧洲标准的 A、B、C、D 级尚有静态限值。我国GMP采用了同欧盟相同的分级标准。设计者应考虑换气率、空气含尘浓度、洁净室自净时间的相互关系。虽然换气率是制药厂暖通空调系统设计中的重要参数,但是,相对于生产房间的分级而言,换气率与自净能力之间有着更紧密的关系,换气率取决于房间尽寸和空气流量任意设定换气率将决定房间的送风量,并影响到工程投资和生命周期成本。
如果已知稳态洁净室内微粒数量、洁净室送风量及送风中微粒含量,即可通过计算得出微粒生成率(PGR),然后可将 PGR 值应用于同类设施的相同生产房间。当采用经验数据进行尘埃粒子时,应考虑正在处理的产品微粒并非污染物,如无菌粉末填充时微粒数较多,这同填充过程相关,并非洁净室设计失败,尽管运行中的设备可产生大量微粒,但操作人员仍是微生物污染的主要来源,加强对人体释放总微粒数的控制即可加强对洁净室内微生物微粒的控制。在保证室内洁净要求的前提下,可以减少房间的送风量,但仍应维持室内温湿度、自净时间、室内空气量平衡等要求。医药洁净室暖通空调系统应能控制空气污染,以保证药品的纯度、均一性和品质;洁净室污染控制通常可通过下述方式实现,即:向工作场所送入经过净化过滤的空气,同环境空气混合并稀释洁净室空气中的污染物。大多数尘埃粒子都不具有生命力,只有一小部份(<1%)微粒具有生命力,比如,它们是可以繁殖的,因此这些带有微生物的活性微粒同不带微生物的微粒一起运动,由此会污染到其它微粒。
由单向流罩流出的空气常比洁净室内空气洁净得多,这部份来自UFH的相对洁净的空气与暖通空调(HVAC)系统的送风共同稀释室内含尘空气;除可减少室内微粒外,UFH 罩内空气还有助于加快洁净室的自净速率;但是在计算房间换气率时,不能将UFH 罩大风量包括在内,过滤后的空气返回进气口仅能在局部区域创造**净环境,因为:这部份空气仅对气流流经的区域产生影响,若罩靠近室内送风口,空气也可从捷径进入UFH罩,无助于在室内混合空气;流出UFH罩的空气可能不如洁净室送风同样洁净,尽管罩下的关键位置可列入A级,但流出空气中可能已带有设备和人员散发的污染物。室内送风口和排风口相对于污染源/热源以及气流障碍物的位置对于污染控制十分重要,可通过调整未端送风口和排风口的位置,使产品和操作人员得到防护。过高的风速可能会在操作人员附近产生漩涡或涡流,增加了在有害物质暴露下的风险。在污染源附近设置局部送风和排风的做法是为有效的。