梁山智远二手化工设备有限公司
联系人:王从奎
电话:13563743569
地址:山东省济宁市梁山县拳铺镇琉璃井村
按本体结构型式分
锅壳式锅炉锅炉的燃烧和吸热蒸发一圆筒体内完成,它有卧式和立式之分,如早期的兰开发、炮仗炉等。水管锅炉主要受热面为管子的锅炉,是早期锅炉的一项重大改进,安全可靠性大大提高。
锅筒式锅炉、锅筒置于火侧之外不受热的锅炉,有双锅筒、单锅筒和多锅筒式,锅筒有横置式、纵置式等。
燃料编辑
工业锅炉用燃料分为三类:
双锅筒水管锅
双锅筒水管锅
固体燃料—烟煤,无烟煤,褐煤,泥煤,油页岩,木屑,甘蔗渣,稻糠等;
液体燃料—重油,清油,渣油,柴油,等;
气体燃料—天然气,人工燃气,液化石油气等 [1] 。锅壳式锅炉锅炉的燃烧和吸热蒸发一圆筒体内完成,它有卧式和立式之分,如早期的兰开发、炮仗炉等。水管锅炉主要受热面为管子的锅炉,是早期锅炉的一项重大改进,安全可靠性大大提高。
锅筒式锅炉、锅筒置于火侧之外不受热的锅炉,有双锅筒、单锅筒和多锅筒式,锅筒有横置式、纵置式等。

④ 锅炉尾部采用热管余热回收技术;
余热是在一定经济技术条件下,在能源利用设备中没有被利用的能源,也就是多余、废弃的能源。它包括高温废气余热、冷却介质余热、废汽废水余热、高温产品和炉渣余热、化学反应余热、可燃废气废液和废料余热以及高压流体余压等七种。根据调查,各行业的余热总资源约占其燃料消耗总量的17%~67%,可回收利用的余热资源约为余热总资源的60%。 **导热管是热管余热回收装置的主要热传导元件,与普通的热交换器有着本质的不同。热管余热回收装置的换热效率可达98%以上,这是任何一种普通热交换器无法达到的。热管余热回收装置体积小,只是普通热交换器的1/3。其工作原理如图所示:左边为烟气通道,右边为清洁空气(水或其它介质)通道,中间有隔板分开互不干扰。高温烟气由左边通道排放,排放时高温烟气冲刷热管,当烟气温度>30℃时,热管被激活便自动将热量传导至右边,这时热管左边吸热,高温烟气流经热管后温度下降,热量被热管吸收并传导至右边。常温清洁空气(水或其它介质)在鼓风机作用下,沿右边通道反方向流动冲刷热管,这时热管右边放热,将清洁空气(水或其它介质)加热,空气流经热管后温度升高。由若干根热管组成的余热回收装置,安装在锅炉烟口,将烟气中热量吸收并高速传导至另一端,使排烟温度降至接近而减少热量排放损失。加热后的清洁空气可烘干物料或补充到锅炉内循环使用。提高锅炉和工业窑炉的热效率,降低燃料消耗,达到节能的目的。
在工业燃油、燃气、燃煤锅炉设计制造时,为了防止锅炉尾部受热面腐蚀和堵灰,标准状态排烟温度一般不低于180℃,高可达250℃,高温烟气排放不但造成大量热能浪费,同时也污染环境。热管余热回收器可将烟气热量回收,回收的热量根据需要加热水用作锅炉补水和生活用水,或加热空气用作锅炉助燃风或干燥物料。节省燃料费用,降低生产成本,减少废气排放,节能环保一举两得。改造投资3-10个月回收,经济效益显著。
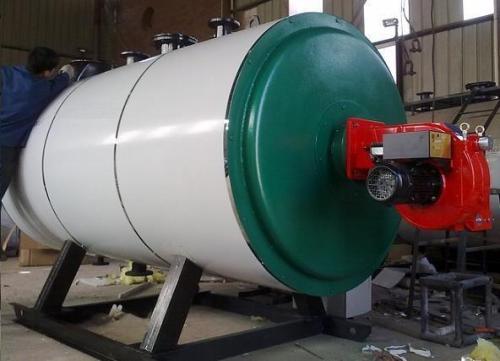
2)频繁吹扫点火
频繁吹扫点火为锅炉沉积着火提供了充足的复燃条件。
锅炉点火过程中烟气流速低,燃烧系统空间的含氧量又较正常运行时高得多,像B炉当时曾连续几次点火吹扫,因此便使尚具余热的未燃尽因具备了充足的过剩氧量而复燃。
(3)爆炸
锅炉爆炸
锅炉爆炸
可燃气体或粉尘与空气形成的混合物在短时间内发生化学反应,产生的高温、高压气体与冲击波,**过周围建筑物、容器、管道的承载能力,使其发生破坏,导致人身、设备事故,称为爆炸事故。
通常说,发生爆炸要有三个条件,一是有燃料和助燃空气的积存;二是燃料和空气的混合物的浓度在爆炸极限内;三是有足够的点火能源。天然气的爆炸下限约为5%,煤粉的爆炸下限是20~60g/m3,爆炸产生的压力可达0.3~1.0MPa。就锅炉范围而言,质是指天然气、煤气、石油气、油雾和煤粉;构成爆炸事故的有炉膛放炮、煤粉仓爆炸及制粉系统爆炸 [7] 。
锅炉满水的处理:
冲洗水位表,确定是轻微满水还是严重满水。
方法:先关闭水位表,水连管旋塞,再开启放水旋塞,如能看到水位线从上下降,表明是轻微满水,停止给水,开启排污阀,放至正常水位 [6] 。
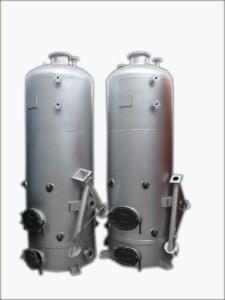
节能改造编辑
锅炉和辅机的节能减排技术锅炉辅机配套设备是实现燃烧介质、燃火、燃烧、燃尽和物料流动匀畅的基本点 ,同时是技术上节能环保的基础。工业锅炉以燃煤为主 ,燃煤工业锅炉以高温链条炉排锅炉为主 ,因此 ,链条炉排锅炉是节能环保的主观 ,也是工业锅炉节能环保的弊端。对链条炉排锅炉而言 ,节能环保的必须围绕着减少机械不完全燃烧损失和排烟热损失两个途径:一是从燃烧设备和燃烧室结构设计上强化煤的引燃、燃烧、燃尽和传热技术 ,包括创新炉排片和配风结构 ,炉拱和二次风强化着火、燃烧和燃尽技术 ,减少灰渣和飞灰含碳量的再燃、燃尽技术 ,主要任务是减少机械不完全燃烧损失 ,如降低灰渣含碳量 ,需要从炉拱设计搭配、二次风调整、炉排片设计、配风均匀性四个方面进行优化设计。