西双版纳钢构热轧H型钢报价 国标H型钢
价格:3680.00起
产品规格:
产品数量:
包装说明:
关 键 词:西双版纳钢构热轧H型钢报价
行 业:钢铁 建筑钢材 特殊/专业建筑钢材
发布时间:2021-06-15
H型钢的种类
根据使用要求及断面设计特性,通常H型钢分为两大类:一类是作为梁型建筑构件用的H型钢;另一类是作为柱型(或桩型)建筑构件的H型钢。作为梁型构件的H型钢,其高度与腿宽之比为2∶1~3∶1,其规格一般从100mm×50mm~900mm×300mm。作为柱型构件的H型钢,其高度与腿宽之比为1∶1,其规格一般从100mm×100mm~400mm×400mm。H型钢高度80~1100mm,腿宽46~454mm,腰厚2.9~78mm,单重6~1086kg/m。

H型钢生产线的平面布置类型 20世纪60年代以后,建筑业对H型钢用量的迅速增加,促进了H型钢厂的兴建和H型钢轧机的制造。据统计,1990年以来世界上大约有近100多套H型钢轧机,其中日本多。 目前世界上H型钢轧机的布置方式主要有两类:一类是半连续布置;另一类是全连续布置。采用半连续布置比较典型的是日本川崎公司水岛中型厂,其产品规格为H100~400mm,主要设备包括2架二辊式开坯机、4架轧机和2架轧边机。全连续布置方式是的,其典型厂有美国1970年建成的宽边H型钢厂、德国萨克公司的中型厂和日本1972年投产的君津大型厂。君津大型厂产量高,工艺设备,其生产规格为100~500mm,主要设备有4架二辊式粗轧机组、7架轧机及4架轧边机。 作为H型钢轧机的主体设备,轧机近年来发展很快,大有取代老式二辊或三辊轧机的趋势。轧机可分为两类:一种是普型材及H型钢联合轧机;一种是H型钢轧机。以**种为多,它可生产许多品种,生产灵活性大,不仅可生产H型钢, 而且还可生产重轨、圆钢、方钢、槽钢和板桩等。 H型钢的主要生产缺陷类型 为便于区别各类缺陷和分析其产生的原因,按工艺流程,钢材缺陷可以分为钢质缺陷、轧制缺陷和精整缺陷类。下面将按此类对H型钢常见缺陷一一阐述。 H型钢常见的钢质缺陷 (1)夹杂。 夹杂是指在H型钢的断面上有肉眼可见的分层,在分层内夹有呈灰色或白色的杂质,经低倍或高倍检验,这些杂质通常为耐火材料、保护渣等。造成夹杂的原因是在出钢过程中有渣混入钢液,或在铸锭过程中有耐火材料、保护渣混入钢液。夹杂会破坏H型钢的外观完整性,降低钢材的刚度和强度,使得钢材在使用中开裂或断裂,这是一种不允许有的钢材缺陷。 (2)结疤。 结疤是一种存在于钢材表面的鳞片状缺陷。结疤有与钢材本体连在一起的,也有不连为一体的。造成结疤的主要原因是浇铸过程中钢水喷溅,一般是沸腾钢多于钢。局部、个别的结疤可以通过火焰清除挽救,但面积过大、过深的结疤对钢材性能影响较大,一般只好判废。 为防止带有结疤的钢坯进入轧机,通常采用火焰清理机清理钢坯表面,或采用高压水将已烧成氧化铁皮的结疤冲掉。在成品钢材上的结疤需要用砂轮或扁铲清除。 (3)分层。 分层是在H型钢断面上的一种呈线纹状的缺陷。通常它是因炼钢浇铸工艺控制不当或开坯时钢锭缩孔未切干净所致。在分层处夹杂较多,尽管经过轧制也不能焊合,严重时使钢材开裂成两半。分层使钢材强度降低,也常常造成钢材开裂。带有分层的H型钢通常要挑出判废。分层一般常出现在模铸相当于钢锭头部的那段钢材中,或发生在用支连铸坯或后一支连铸坯所轧成的钢材上。 (4)裂纹。 H型钢裂纹主要有两种形式:一种为在其腰部的纵向裂纹;另一种为在其腿端的横向裂纹。腰部的纵向裂纹来自浇铸中所形成的内部裂纹,腿端的横向裂纹来自钢坯或钢锭的角部裂纹。无论是哪种裂纹均不允许存在,它都破坏钢材本身的完整性和强度。 H型钢常见的轧制缺陷 (1)轧痕。 轧痕一般分为两种,即周期性轧痕和非周期性轧痕。周期性轧痕在H型钢上呈规律性分布,前后两个轧痕出现在轧件同一部位,同一深度,两者间距正好等于其所在处轧辊圆周长。周期性轧痕是由于轧辊掉肉或孔型中贴有氧化铁皮而造成的在轧件表面的凸起或凹坑。非周期性轧痕是导卫装置磨损严重或辊道等机械设备碰撞造成钢材刮伤后又经轧制而在钢材表面形成棱沟或缺肉,其大多沿轧制方向分布 。 (2)折叠。 折叠是一种类似于裂纹的通常性缺陷,经酸洗后可以清楚地看到折叠处断面有一条与外界相通的裂纹。折叠是因孔型设计不当或轧机调整不当,在孔型开口处因过盈充满而形成耳子,再经轧制而将耳子压入轧件本体内,但不能与本体焊合而形成的,其深度取决于耳子的高度。另外,腰、腿之间圆弧设计不当或磨损严重,造成轧件表面出现沟、棱后,再轧制也会形成折叠。 (3)波浪。 H型钢波浪、可分为两种:一种是腰部呈搓衣板状的腰波浪;另一种是腿端呈波峰波谷状的腿部波浪。两种波浪均造成H型钢外形的破坏。波浪是由于在热轧过程中轧件各部伸长率不一致所造成的。当腰部压下量过大时,腰部延伸过大,而腿部延伸小,这样就形成腰部波浪,严重时还可将腰部拉裂。当腿部延伸过大,而腰部延伸小时,就产生腿部波浪。另外还有一种原因也可形成波浪。这就是当钢材断面特别是腰厚与腿厚设计比值不合理时,在钢材冷却过程中,较薄的部分先冷,较厚的部分后冷,在温度差作用下,在钢材内部形成很大的热应力,这也会造成波浪。解决此问题的办法是:首先要合理设计孔型,尽量让不均匀变形在头几道完成;在精轧道次要力求H型断面各部分腰、腿延伸一致;要减小腰腿温差,可在成品孔后对轧件腿部喷雾,以加速腰部冷却,或采用立冷操作。 (4)腿端圆角。 H型钢腿端圆角是指其腿端与腿两侧面之间部分不平直,外形轮廓比标准断面缺肉,未能充满整个腿端。造成腿端圆角有几方面原因:其一是开坯机的切深孔型磨损,轧出的腿部变厚,在进入下一孔时,由于楔卡作用,所以腿端不能得到很好的加工;其二是在机组轧制时,由于机架与轧边机速度不匹配,而出现因张力过大造成的拉钢现象,使轧件腿部达不到要求的高度,这样在轧边孔中腿端得不到垂直加工,也会形成腿端圆角;其三是在整个轧制过程中侧腹板出现偏移,使得轧件在咬入时偏离孔型对称轴,这时也会出现上述缺陷。 (5)腿长不对称。 H型钢腿长不对称、有两种:一种是上腿比下腿长;另一种是一个腿上腿长,而另一个腿则下腿长。一般腿长不对称常伴有腿厚不均现象,稍长的腿略薄些,稍短的腿要厚些。造成腿长不对称也有几种原因:一种是在开坯过程中,由于切深时坯料未对正孔型造成切偏,使异形坯出现一腿厚一腿薄,尽管在以后的轧制过程中压下量分配合理,但也很难纠正,终形成腿长不对称;另一种是轧机水平辊未对正,轴向位错,造成立辊对腿的侧压严重不均,形成呈对角线分布的腿长不对称。

在许多钢结构项目中,都涉及到钢梁开孔问题,比如吊装孔、吊挂孔、穿筋孔等等,这些都是现场便于施工的措施,或者是其他的构造要求,比如管道支架吊挂点等。而现行设计及施工规范说明应尽量避免型钢翼缘板开孔,这里在分析软件中对几种开孔情况进行简化的计算分析,比较直观的反映开孔对受力情况的影响。
因为不同项目结构形式,受力有差别,下面举一个简单算例来验证这个结论,这里直接取钢框架结构中一种常见的钢梁受力形式:两端固支梁(多为主梁)。
计算模型钢梁跨度取6M,主梁截面取H 400x200x8x12,材质为Q235B。
开孔位置分别取如下位置,尺寸为φ20圆孔。
为使截面强度利用率达到90%,经查表计算得主梁均布荷载值取70KN/m,在支座处负弯矩大,跨中处正弯矩大,弯矩大小:情况1<情况2<情况3。
根据以上条件在软件中建模加载(左图),进行网格划分(右图),网格在孔部位进行加密处理以提高此部位求解精度,后进行计算求解,
可以确认整体计算结果与理论计算基本吻合,翼缘板应力较大处出现在弯矩大的截面,也说明了H型钢翼缘板主要承受弯矩作用,下面观察三种情况的孔位处的应力分布情况:
由于模型建模加载以及计算模型的误差,所得结果数值度仅作为参考,但能一定程度上反映孔周边实际受力过程中出现的应力集中状况,观察三处孔周应力数值分布情况,可见应力集中处应力大小:情况1<情况2<情况3,与实际理论计算弯矩大小分布相吻合。
综上所述,钢梁弯矩大的截面处翼缘板开孔容易出现应力集中处应力大小**限的情况,可能导致钢梁局部塑性屈服破坏,严重的可能导致板材撕裂,这个是需要在设计及施工中应尽量避免出现的情况,如果无法避免则需要做好补强措施,局部加强截面以降低应力集中效应。
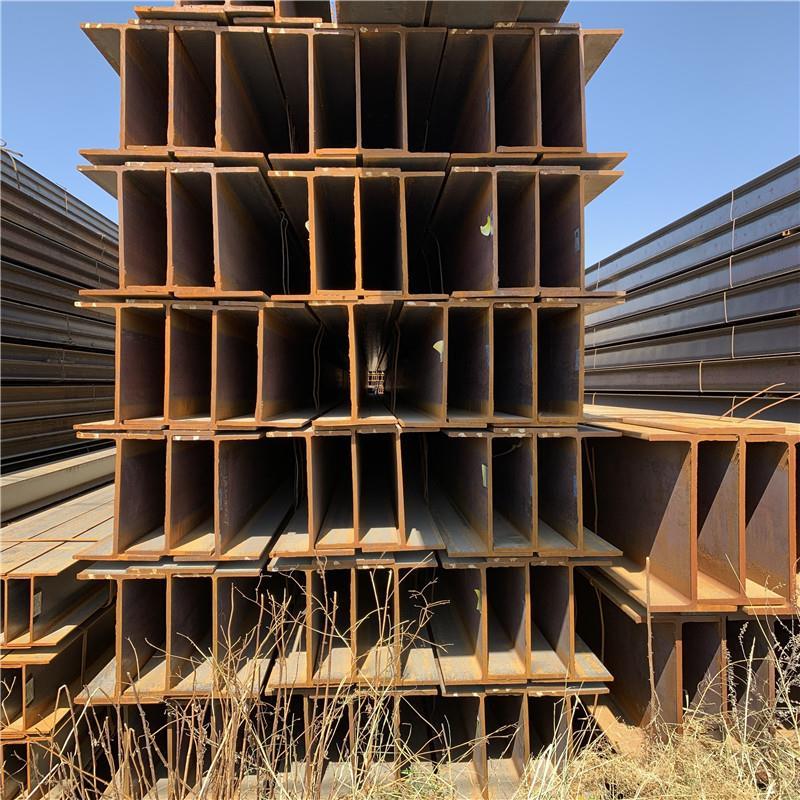
热轧H型钢的优点
H型钢是一种新型经济建筑用钢。
H型钢截面形状经济合理,力学性能好,轧制时截面上各点延伸较均匀、内应力小,与普通工字钢比较,具有截面模数大、重量轻、节省金属的优点,可使建筑结构减轻30-40%;又因其腿内外侧平行,腿端是直角,拼装组合成构件,可节约焊接、铆接工作量达25%。常用于要求承截能力大,截面稳定性好的大型建筑(如厂房、高层建筑等),以及桥梁、船舶、起重运输机械、设备基础、支架、基础桩等。
H-型钢是由工字型钢优化发展而成的一种断面力学性能更为优良的经济型断面钢材,尤其断面与英文字母“H”相同而得名。其特点如下:
→翼缘宽,侧向刚度大。抗弯能力强。
→翼缘两表面相互平行使得连接、加工、安装简便。
→与焊摄工字钢相比,成本低,精度高,残余应力小,*昂贵的焊接材料和焊缝检测,节约钢结构制作成本30%左右。
→相同截面负荷下.热轧H钢结构比传统钢结构重量减轻15%-20%。
→与砼结构相比,热轧H钢结构可6%的使用面积,而结构自重减轻20%一30%,减少结构设计内力。
→H型钢可加工成T型钢,蜂窝梁可经组合形成各种截面形式,较大满足工程设计与制作需求。
H型钢主要用于工程,厂房设备,机械设备,桥梁,高速公路,民房等;机械性能和物理性能好,牢固,节约能源和环保的效果。H型钢是一种经济型断面钢材,广泛用于工业、建筑、桥梁、石油钻井平台等方面,据预测2005年我国H型钢需求量约250万吨,2010年需求量500万吨,但目前我国H型钢年生产能力为120万吨,市场需求量非常巨大。