东莞万级洁净室装修 电子厂生产车间工程
价格:1500.00起
产品规格:
产品数量:
包装说明:
关 键 词:东莞万级洁净室装修
行 业:生活服务 装修装饰 厂房装修
发布时间:2021-02-21
无菌药品生产车间的改造设计探讨
| 原车间存在的问题及改造思路
1.1 工艺改造1.1.1 原灌装间进入与退出共用一个缓冲间,存在交叉污染问题。改为增加单独的退出通道至D 级走廊,并设压差梯度保护。1.1.2 原配液由人工完成,存在效率低、污染风险的问题。改为增加独立配液间,并增加自动配液系统,设层流罩保护。1.1.3 原称量与配液在同一间房间完成,存在交叉污染风险。改为增加独立称量间,完成称量。1.1.4 原灌装间百级面积过大,存在能耗大、难控制的问题。改为B 级背景+灌装区A 级层流保护,灌装机设置围挡。1.1.5 原冻干后成品由人工手持托盘转运,存在效率低、污染风险的问题。改为增加小车进行转运。1.1.6 原轧盖后至包装采用人工转运的方式,效率低、且无直接转运通道。改为转盘转运,并将轧盖背景区域洁净级别提升为C 级。1.1.7 原轧盖机没有抽风装置,也没有自动剔除装置,容易形成二次污染。改为替换轧盖机带抽风、自动剔除装置。1.1.8 原轧盖没有排风,容易形成二次污染,改为增加排风。1.1.9 原两间洗衣间存在功能重复。改为将其合并,增加大功率洗衣烘干机。1.10 原车间缺少在线粒子检测间及设备,改为增加独立的在线粒子检测间及设备。1.11 原车间缺少可在灌装间外部观察灌装操作的观察窗,改为在灌装间与准备间之间增加观察窗。1.2 空调系统改造1.2.1 原车间时常出现温湿度**标现象。经调查,空调设备管路、盘管堵塞,并存在滴漏现象,空调箱面板锈蚀严重,夏季表面结露。综合考虑,将空调箱全部更换。
1.2.2 原车间时常出现压差过低、关键区域压差梯度不够的问题。经调查,送回风阀门有松动现象,定位机构生锈腐蚀严重,难以调整。部分风管内壁锈蚀,堵塞过滤器,造成压差不稳定。改造后将其全部更换。1.3 其他改造原车间工艺排水缺少放倒流措施。改为将工艺排水集中排放,增加空气隔段措施。
-02-
| 设计需要遵循的规范
设计需符合《药品生产质量管理规范(2010 年修订)》、《洁净厂房设计规范》、《医药工业洁净厂房设计规范》、《建筑设计防火规范》。《药品生产质量管理规范(2010 年修订)》与98 版的《药品生产质量管理规范》对于无菌药品生产有着明显的不同,主要区别见表1。
-03-
| 设计方案
3.1 空调系统的基本形式采用全空气系统,由室外取新风经粗效过滤器与室内回风在空调箱内混合,经表冷器降温除湿,再经风机增压送入加热段再热、加湿段加湿,经过中效过滤器二级过滤送至端过滤器进行过滤。室内洁净度由粗、中、过滤器保证。温湿度由表冷器、加热盘管、加湿器控制。送风机提供必要的送风量,保证房间换气次数。调节送风机、送回风阀调节房间压差。
3.2 空调系统划分按照洁净级别设置空调箱。即每个级别对应独立的空调箱。并将净化空调与非净化空调分别设置。3.3 过滤器的设置净化空调箱内粗效采用G4 袋式过滤器,中效采用F8袋式过滤器,末端采用A/B 区采用H14(过滤效率 99.995%@0.3μm),C/D 区采用H13(过滤效率99.99%@0.3μm)。非净化空调箱内粗效采用G4 袋式过滤器,中效采用F7 袋式过滤器。排风箱内采用F7 中效过滤器。3.4 压差梯度设计按照GMP 要求,洁净区与非洁净区之间、不同级别洁净区之间的压差应当不低于10 Pa。进入洁净区的个房间设为净化保护区,压力为0 Pa~5Pa,*二个房间压力为15 Pa。相同级别房间压力依次递增,使非净化区至走廊形成由小到大的阶梯式压差梯度。灌装间和走廊之间的缓冲间采用下沉式压差梯度(非阶梯式),主要考虑到灌装区为核心区域,既要保证其压力,免受外部污染,也要保证灌装时产生的雾滴扩散至C、D 区,所以采用下沉式压差梯度。洁具间、灭菌间轧盖间采用相对负压,防止热湿、铝屑等颗粒扩散。3.5 送风量、排风量、回风量、新风量设计送风量应满足以下三个要求,并取三者大值。(1)室内洁净度。(2)室内温湿度。(3)室给的新风量。为简化计算,送风量采用推荐值估算。根据《洁净厂房设计规范》、《药品生产质量管理规范(2010年修订)》,如表 2 所示。
后,校核系统、房间的风量:系统送风量=系统新风量+系统回风量=系统回风量+系统排风量;房间送风量=房间回风量+房间排风量。3.6 负荷计算3.6.1 冷负荷(1)采用不稳态法逐一计算每一个系统每一时刻的冷负荷,确定综合值。(2)根据系统风量计算每一个空调系统的制冷量。(3)校核:系统风量计算的制冷量应大于或等于不稳态法算的综合值。3.6.2 热负荷(1)采用稳态法逐一计算每一个系统的热负荷。(2)根据系统风量计算每一个空调系统的制热量。(3)校核:系统风量计算的制热量应大于或等于稳态法计算的热负荷。3.6.3 加湿量根据系统风量计算每一个空调系统的加湿量。3.7 材料选择洁净室空调系统的材料应具有耐腐蚀、使用寿命长、性能稳定、不产尘屑的特点。故风管采用热镀锌钢板制作,阀门采用碳钢喷塑,风口采用冷轧钢板喷塑,空调箱外壁采用彩钢板,内壁采用不锈钢。
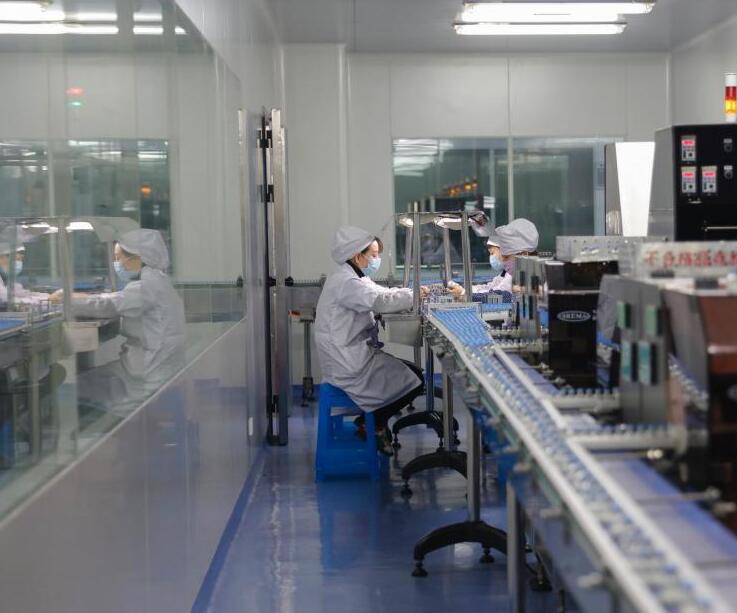
无菌药品制作车间 装修净化
中间产品无菌检查阳性结果及溯源分析举例
2012年度共收检乙型脑炎减毒活疫苗中间产品无菌检查1731批次,其中阳性结果35 批次,占2.02% 。经分离纯化培养和菌型鉴别分析,主要存在里拉/藤黄微球菌、蜡样芽胞及奇异变形菌等,举例溯源分析如下:
①里拉 /藤黄微球菌检出3例。里拉/藤黄微球菌为洁净区环境及人员监测主要菌群,而在水系统样品中并未检出,故推断为操作过程中经环境带入;
②蜡样芽胞检出3例。蜡样芽胞在水系统中全年仅检出1次,而在环境监测中检出83次(占11.05%)。蜡样芽胞的生长温度范围为20~45℃,10℃以下生长缓慢或不生长,50℃时不生长,在100℃下加热20min即被破坏。而所有的工艺用水均经过高压灭菌(121℃,30min)处理。因此推断,蜡样芽胞应仍为操作过程中经环境带入;
③奇异变形检出4例,由于截止目前洁净区环境及人员和水系统微生物数据库中均未曾检出此类菌,故排查分析只可能是工艺操作本身引入。据查阅资料,奇异变形一般广泛存在于水、土壤的**物以及人和动物的肠道。故根据工艺操作特点进行推测,很可能来自无特定病原体(Specific pathogen free,SPF)级实验地鼠取肾操作工艺。故对此批工艺剩留的末次肾块洗涤液取样进行无菌检查检测,证实为SPF地鼠取肾操作不慎带入。
讨论
从菌型分析结果统计可知,该洁净区环境和人员主要存在革兰阳性球菌如里拉/藤黄微球菌、表皮葡萄球菌、人葡萄球菌等,共占78.56% 以上,其次为蜡样芽胞和少量的库克菌及霉菌等。另外,对于霉菌从检测时间和空间上看,主要集中出现在春、夏季节,洁净区较潮湿的精洗场和细胞水浴加温洁净室。因此宜在春、夏季节加强工艺湿度较大洁净室霉菌的消杀处理。
封闭的用水(80℃保温循环)和纯化水(20℃保温循环)管道环境条件较差,检出的微生物种类和数量均较少,经鉴别分析主要存在少动鞘氨醇单胞菌、皮氏罗尔斯顿菌等革兰阴性菌以及芽胞等。
溯源分析举例表明,根据初步建立的微生物数据库以及中间产品无菌检查阳性菌型分析结果可以比较明确地确定产品污染的来源,2012 年乙型脑炎减毒活疫苗中间产品无菌试验阳性结果,主要为操作过程中经环境偶然带入以及地鼠取肾操作不慎带入。
虽然该中间产品并不是无菌工艺操作(半成品配制时需经0.22μm薄膜过滤),但尽量控制本底污染对于实施GMP控制具有积极的意义。奇异变形全年检出4例,且无菌检查时均能在观察结果前2~3d就发现样品染菌(无菌检查孵放要求是培养14d),相关批次单一收获物均报废处理。从无菌风险和生产成本来看,该产品工艺中取肾操作是需关注的重点,可通过加强员工现场操作培训和考核以及进一步优化该步工艺操作等实现。
另外,2012年中间产品无菌检查阳性结果还检出放射根菌、苛养颗粒链菌、斯氏普罗威登斯菌等少数微生物种类,全年各仅检出一例,且暂未在建立的洁净区微生物数据库中出现,目前还无法确切地追溯其来源。
由于全面开展菌型分析工作仅一年多时间,且乙型脑炎减毒活疫苗工艺较为复杂,涉及到SPF 地鼠操作,今后将根据工艺特点建立SPF地鼠如肠道、皮毛等部位的微生物基础数据库,以完善来源追溯途径,进一步提高GMP操作水平。
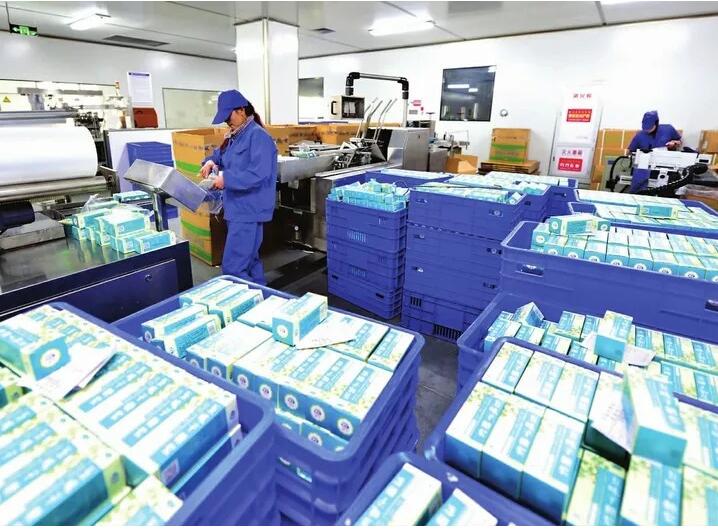
医药无菌车间——洁净板项目工程案例
项目名称:济南瑞康医药无菌车间
应用板材:洁净板
应用系统:直接粘贴
施工时间:2017年6月
简 介:济南瑞康医药有限公司位于 临港经济开发区机场路东侧,是瑞康医药股份全资子公司。无菌车间装修项目使用墙冠UV氟碳洁净板共计2000㎡。
洁净板特性
1.防火
洁净板用特种硅酸钙板作为基板,燃烧性能达到GB8624A1级标准要求。当室内发生火灾时,能有效阻止火势的蔓延,不会产生有毒烟雾,无火焰传递;
2.环保
产品释放量符合GB18580-2001E1级,生产过程不使用任何溶剂,可挥发性**物(氡)<200Bq/m3,无氨,无笨,放射性达到A类装修材料标准。不含石棉;
3.
洁净板具有良好的性,抵抗多种病菌(大肠、金葡萄球菌、白色)在板材表面的存活;
4.耐腐蚀
洁净板具有相当的抵抗和二等各类腐蚀性物质的耐腐蚀性能,具有较强的耐酸、耐碱、的特性,包括各类清洁剂、消毒液及其它等;
5.耐候
基板品越,涂层经过十一次紫外光固化工艺,板材耐候性能强,使用寿命长达25年以上。具有防辐射、抗静电性能。

制药无菌车间洁净车间装修设计
随着不断循环每次去除水分越来越少,干燥间内湿度越来越低。以此方法可以将干燥间内湿度降到20% 以下,达到器皿干燥的目的。
2.4.2 合理的加热及保温温度设计
从表1 中可以看出,提高干燥间保温温度达60℃,吸收器皿中水分,设置循环同样时间达到湿度80%,空气中水分为103.7g/m3,一次排放水量可达(103.7g/m3-11.4g/m3)x120 g=11076g,是保温45℃情况4896g 的1 倍以上,除湿效率更高。可见,干燥间的保温是很关键的。
但因为干燥间周围的洁净厂房温度一般为20℃,如果干燥间温度设置过高,温差太大,散热也很大,热损失较大,需要的加热功率过大,加热段温度太高,安全风险过大,故一般保温循环温度设定在45℃-60℃较好。通常冬季设为45℃,夏季设为60℃。
由表1,可知即便是湿度达到,室外温度15℃时, 大气中水分含量为m1=12.7g/m3。加热循环至45℃, 多次置换排放后湿度为20%,空气中水分含量为m2=13.0g/m3,m2>m1,说明此时通过纯加热除湿方式可以实现终湿度低于20% 的结果。
2.5 综合干燥除湿
2.5.1 综合干燥除湿的原因
夏季较端情况下,室外温度35℃以上,湿度 时,查表1 可知,此时空气中水分含量将>40g/m3。如单纯用加热排放,对应40g/m3的水分含量,干燥间内循环温度45℃,湿度> 60%;循环温度50℃,湿度接近50%;55℃,湿度接近40%;即便温度达到60℃湿度也**过30%,此时难于达到干燥的目的。
所以,在夏季较端情况下,置换室外空气时,应该对室外高温高湿空气首行降温除湿,使空气中水分含量由40g/m3先降至15g/m3-20g/m3, 去除多25g/m3水分, 再加热升温循环至对应5055℃-55℃,即可将终湿度控制在20% 以下,达到干燥的目的。
2.5.2 表冷器制冷量的计算
根据前面所述,新风补风量V=2500m3/h,新风中水含量M=40g/m3,单位时间处理水量m=MV,=2500m3/hX40 g/m3=100Kg/h
过程中需要将35℃新风降至10℃, 温差ΔT=25℃
水热容量C=1cal/g℃,
需要冷量Q=mCΔT=100Kg/hX1cal/g℃X25℃=2500Kcal/h
再考虑表冷器的交换效率如果为50%,则冷量需要量应为5000 Kcal/h。
3 程序控制
洁净除湿干燥系统的运行,涉及新风、送回风风阀开关、温湿度采集、空气中水分含量、时间参数计算对比控制、加热、制冷、风机无风保护、过热保护、各种运行方式切换等控制,所以我们选用了西门子S7-200PLC 编程控制器,并通过网络与系统连接,可以实现在线和远程双重控制。
参考文献:
[1] 国家食品药品监督药品认证管理中心;药品GMP 指南 厂房设施与设备[M]. 北京: 中国医药科技出版社,2011.8
[2] *共和国令*79 号. 药品生产质量管理规范(2010年修订)[EB]. 北京: ,2011.1
[3] 刘先哲,蔡志明;干燥洁净车间的设计、施工与调测;洁净与空调技术[J];1997.3 期.
[4] 王军;制药厂洁净车间空调通风设计体会;建筑热能通风空调[J];1998.2.
[5] 徐砾;GMP 实施过程中洁净车间的设计和管理;化学与生物工程[J];2003.4.
[6] 陈光建;从生产管理理论看药厂洁净车间的GMP 设计;医药工程设计[J];2001.1.
[7] 万斌;蔡智辉、詹彦敏;GMP 洁净车间的空调节能控制改造;[J] 电工技术;2009.12 期.