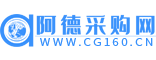
价格:88.00起
上海轩本实业有限公司
联系人:钱经理
电话:18116413584
地址:上海市宝山区市一路199号1楼1285A
热镀锌镀层的组织结构钢带连续热镀锌过程中,各种相层的形成过程尚不完全明了。目前存在两个观点,一种观点认为,当钢板与熔融的锌液接触时,先形成锌在a-Fe中的固溶体,当锌在固溶体中达到饱和浓度时,由于两种元素的互相扩散,便形成铁含量较高的r相。由于铁原子通过r相向外部扩散,便开始形成铁含量稍低的61相层,在一边的热镀锌生产过程中,1相层较厚,此相层包括两个区域,即与T相层和邻的致密区,其结品的生成速度大于其生长速度,故在此区域中结品颗粒细小而致密;在此区域的外部是一层组织疏松的区域,其结品的生长速度小于其成长速度,故其晶粒扭大且疏松,从FcZn二元系状态图中可以看出,31相稳定存在范围是从室温到640℃,靠近r相的区域,0相的铁含量约为11,5%,靠近相的区域,b和的铁含量约为7%,由于1相的疏松区域存在空隙,锌液容易通过空欧诊入,与相反应,形成铁合量更低的相层。夕相品体呈针状,组织疏松,在较高温度下镀锌时,和会部分地从此合金层上脱落而悬浮于锌液中Galvalume的层组织结构Galvalume合金坡层与热镀锌相比,合金镀层的相对密度小(3.75),在同样镀层厚度时,镀层金属的消耗只有镀锌的1/2,铝的质量比还是体积比都比度约为21~32ym,分为内外两层,见图2-4[40妈层复杂得多,其镀层平均厚大,所以这种镀层更接近镀铝层的结构,但要比镀外层为AZn合金层,厚度约为18~26μm,其成分与镀液大休相同,其组织又有两项组成,一项为大量的铝先结品形成较细的树枝状晶组织,构成了整个镀层的网络骨架,体积约占80%,另一项为分布在树枝状品空欧内的伪共品富锌相,体积约占20%,见图25对外层进行X射线衍射试验,从图2-6(a)中可以看到,在外层除了锌铝的线条外,还存在0相(Fealy化合物),n相(Fe2Al化合物)和H相(aFalsi化合物)的相应线条,其中,锌和铝行射线条的相对强度较高,与ASTM粉末行射卡图2-5Galvalume外层组织(100×)中的整个a值谱线几乎全部对应。由此可以认为,外层主要组成部分为富铝a固溶体,同时含有微量的0相、n相、H相。内层为金属间化合物,由fe-al-zn-si四元合金组成,这一层的Zn较少,而大部分Si存在于此合金层当中。该层的厚度对镀层黏附性能和延伸性能起决定性作用,为2~4pm、若内层太厚,会引起镀层黏附性能和延伸性能的下降。与外层不同,内层H相,0相衍射线条有较大程度的增加,Zn、Al的相应谱线则少得多,所以该层主要由H相、0相组成,而H相、0相大部分分布在靠近外层一倒,向内部延伸时明显减少,见图2-6(b)整个镀层中,A1和Zn的分布基本上是均匀的,外层中Fe、Si元素的含量远低于在内层中的含量。在内、外层交界的地方Si和Fe元素含量高,外层中的属色条状物是富硅相。有资料表明组成相的化学成分平均值如表22所列。热浸镀产品的分类按热镀锌工艺及件类型不同,热镀锌可分为钢带连续热镀锌(continuoushot-dipgalvanizing)和批量热镀锌(batchhot-dipgalvanizing)两大类。钢带连续热镀锌是冷轧(热轧)钢带(卷)在连续生产线上进行热浸镀锌,钢带(卷)一般通过开卷、剪切、焊接,碱或电解清洗,活套存料,加热退火和还原,热浸锌、气刀控厚、镀层的锌花或合金化处理,冷却、光整和拉矫、钝化、活套存料、涂油、卷取或剪切等一系列工序,生产出热镀锌钢带卷或称热镀锌钢板。连续热绽锌钢板具有理想的耐蚀、成型、涂装等综合性能和成本低、外观好等优点,主要应用于建筑、汽车和家电行业,是近十几年来发展得较快的钢材品种之一。图2-7所示为典型的美钢联法钢带连续热镀锌生产线工艺布置简图。批量热镀锌是将钢结构制件等材料分批次浸入锌锅中获得热镀锌件的方法按工艺特点分类按照热镀锌生产工艺特点,可分为在线退火和线外退火两大类型,在线退火热镀锌一般采用氢气还原法,而线外退火采用熔剂法,如表2-3所列。E线外退火的熔剂法又可分为湿法和干法。湿法主要用于单张钢板热镀锌,而干法中除了用于单张钢板和零部件批量热镀锌外,还有惠林法和里赛特可用于钢带连续热饺锌在线退火的氢气还原法均用于钢带连续热镀锌,这其中包括森吉米尔法,改良森吉米尔法、美国钢铁公**(美钢联法)、赛拉斯法以及莎伦法五种.在氢气还原法连续热镀锌生产线上的工艺段上有连续退火炉装置,它可使冷轧钢带直接进入镀锌生产线进行在线退火,同时进行钢带表面的还原处理,这就将钢带退火与表面还原两工艺在一个炉中完成,使工艺过程简化,大大降低了镀锌成本.塞拉斯法塞拉斯法的原料钢带可以是经罩式退火炉退火的或者直接采用冷轧的钢带。钢带的前处理与惠林法相同,即经过脱脂酸洗,后经烘干预热后进入立式退火炉,此炉的特点与其他连续热镀锌不同,采用煤气燃烧的直接火焰加热钢带为使燃烧产物具有一定的还原性而采用严格控制炉内气氛(煤气和空气比小使煤气不完全燃烧,燃烧废气呈还原性成分(见表2-5),可将钢带表面微薄的氧化膜还原,同时在高达1000~1250℃的炉膛温度下进行再结晶退火,后在低H2含量(15%左右)的冷却段内冷却到镀锌温度,通过炉鼻进入锌锅中镀锌图2-13所示为赛拉斯法退火炉及冷却段的剖面示意图如果采用已退火的钢带作为原料,则钢带在还原炉内可加热到500~520℃而不必加热到再结品温度。赛拉斯法虽然产量较高(50t/h),机组短小,设备紧凑,投资费用低,但其工艺过程复杂,有污染,且当机组停止运行时必须将钢带移出炉外,否则钢带易被高温退火炉烧断,等等,由于存在这些缺点,使得该方法未得到广泛的应用。线外退火熔剂法分活面收过平钢与流触发生底底今周段解表面十污和氧化膜等,还要确保在浸镀前其表面不重新被氧化。可采用的方法之一是在纲材表面涂以熔剂,例如常用的熔剂有NHC、ZnCl2以及其复盐水溶液为获得适于镀锌的洁净而活化的钢板表面,必须对其进行充分的脱脂,除掉表面的油污,钢板表面的油膜能阻止酸洗时氧化铁膜的清除,同时也严重影响水熔剂膜的均匀涂覆。这是造成镀锌层连续性变坏的重要原因。钢板的脱脂一般采用高温的碱液,现在多改用高效的金属清洗剂进行,其除油效果好,用量少并可在常温下进行钢板表面的氧化皮和氧化膜多用10%~20%H2SO4或HCl进行清除,其中添加少量缓蚀剂、抑雾剂更有利于酸洗。硫酸**、浓度高,但需在较高温度(55~60℃)下进行,且其酸洗产物黏附于钢板表面,水洗时难以除尽,必须再用稀盐酸漂洗。而用盐酸酸洗,钢板表面酸洗质量好,呈灰白色外观。酸洗时应注意掌握程度,进免过酸洗与欠酸洗。欠酸洗时钢表面氧化膜去除不尽,钢板表面不能完全活化,给以后的熔剂处理造成困难;酸洗过度,则钢板发生局部过腐蚀,出现麻坑和气泡,而不利于获得好的镀锌层质量(锌层出现白色道痕).酸洗程度的掌握与酸液浓度、Fe3+含量、温度、时间及钢板表面状况和化学成分有关,这些都需要操作者凭其操作经验加以控制。在涂水溶液熔剂时,混法镀锌对此过程要求不十分严格,而干法镀锌的要求十分严格。首先要求酸洗后的残余Fe盐[Fe2(SO4)3或FeCl2]等要充分水洗除去。通常在稀盐酸处理后,还需用高压水喷射冲洗和热水冲洗。其次要达到所涂的熔剂层在钢板表面完全连续,无熔剂斑痕,厚度适当且均匀,熔剂中不含杂质尘士等污物。为此,应保持水熔剂的密度一定。涂覆熔剂的双辊表面状态及钢带表面的光洁度是决定熔剂层厚度和均匀性的关键。对于表面光滑的冷轧板涂熔剂时,涂熔剂的辊子表面必须粗化,即生成细纹(纹的宽度及深度视所需熔剂层的厚度而定)。由于此熔剂层不易直接测量,一般凭经验调节,以均匀不产生流淌为宜熔剂层的烘干是钢板熔剂法热镀锌取得良好镀锌层至关重要的环节。由于ZnC2含结品水(ZnCl2.H2O),当烘干时,烘干温度过低(板温低于150℃)此结晶水难以排除,造成熔剂不干,在出锌锅时易出现粘辊现象,使纯锌层粗糙不光滑。但烘干温度过高(板温**220℃)则熔剂挥发,引起钢板表面氧化,从而造成局部大面积漏镀。为将熔剂彻底烘干,烘干炉内必须及时移走产生的水蒸气。因此,改善炉内的通风条件也是十分重要的。在钢板烘干后进入锌锅前,应及时扒除锌液表面的浮渣,特别要注意扒除导向杆根部的浮渣,否则钢板的前端容易黏附此浮渣而影响镀锌层外观质量此外,保持镀锌辊表面均匀包覆一层锌液,不黏附浮渣、熔剂渣等物也是取得锌层良好外观质量的重要环节。如有上述不洁物黏附应及时清除。熔剂法单张热镀锌板机组速度大为10m/min,生产率很低,为2~3t/h,耗锌量为90~100kg/t,锌渣及锌灰生成量为6~12kg/t。因此其生产成本高且表面质量也差一些,同时,酸洗的酸雾弥散在整个车间,操作环境恶化。三废的处理问题严重。因此,熔剂法的热镀锌工艺后来逐渐被污染小、产量高、成本低、质量好的连续热镀锌所代替。