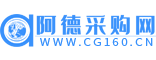
价格:5500.00起
余姚市优职模具厂
联系人:周老师
电话:15669150888
地址:浙江省宁波余姚市凤山街道中山北路1395号
三、影响模具结构及模具个别系统的因素很多,很复杂:
1、型腔布置。根据塑件的几何结构特点、尺寸精度要求、批量大小、模具制造难易、模具成本等确定型腔数量及其排列方式。对于注射模来说,塑料制件精度为3级和3a级,重量为5克,采用硬化浇注系统,型腔数取4-6个;塑料制件为一般精度(4-5级),成型材料为局部结晶材料,型腔数可取16-20个;塑料制件重量为12-16克,型腔数取8-12个;而重量为50-100克的塑料制件,型腔数取4-8个。对于无定型的塑料制件建议型腔数为24-48个,16-32个和6-10个。当再继续增加塑料制件重量时,就很少采用多腔模具。7-9级精度的塑料制件,多型腔数较之指出的4-5级精度的塑料增多至50%。
2、确定分型面。分型面的位置要有利于模具加工,排气、脱模及成型操作,塑料制件的表面质量等。
3、确定浇注系统(主浇道、分浇道及浇口的形状、位置、大小)和排气系统(排气的方法、排气槽位置、大小)。
4、选择**出方式(**杆、**管、推板、组合式**出),决定侧凹处理方法、抽芯方式。
5、决定冷却、加热方式及加热冷却沟槽的形状、位置、加热元件的安装部位。
6、根据模具材料、强度计算或者经验数据,确定模具零件厚度及外形尺寸,外形结构及所有连接、定位、导向件位置。
7、确定主要成型零件,结构件的结构形式。
8、考虑模具各部分的强度,计算成型零件工作尺寸。
以上这些问题如果解决了,模具的结构形式自然就解决了。这时,就应该着手绘制模具结构草图,为正式绘图作好准备。
四、绘制模具图
1、要求按照国家制图标准绘制,但是也要求结合本厂标准和国家未规定的工厂习惯画法。在画模具总装图之前,应绘制工序图,并要符合制件图和工艺资料的要求。
2、由下道工序保证的尺寸,应在图上标写注明"工艺尺寸"字样。如果成型后除了修理毛刺之外,再不进行其他机械加工,那么工序图就与制件图完全相同。
3、在工序图下面标出制件编号、名称、材料、材料收缩率、绘图比例等。通常就把工序图画在模具总装图上。
4、绘制总装结构图:绘制总装图尽量采用1:1的比例,先由型腔开始绘制,主视图与其它视图同时画出。
五、模具总装图应包括以下内容:
1、模具成型部分结构。
2、浇注系统、排气系统的结构形式。
3、分型面及分模取件方式。
4、外形结构及所有连接件,定位、导向件的位置。
5、标注型腔高度尺寸(不强求,根据需要)及模具总体尺寸。
6、辅助工具(取件卸模工具,校正工具等)。
7、按顺序将全部零件序号编出,并且填写明细表。
8、标注技术要求和使用说明。
六、模具总装图的技术要求内容:
1、对于模具某些系统的性能要求。例如对**出系统、滑块抽芯结构的装配要求。
2、对模具装配工艺的要求。例如模具装配后分型面的贴合面的贴合间隙应
不大于0、05mm模具上、下面的平行度要求,并指出由装配决定的尺寸和对该尺寸的要求。
3、模具使用,装拆方法。
4、防氧化处理、模具编号、刻字、标记、油封、保管等要求。
5、有关试模及检验方面的要求。
七、绘制全部零件图
由模具总装图拆画零件图的顺序应为:先内后外,先复杂后简单,先成型零件,后结构零件。
1、图形要求:一定要按比例画,允许放大或缩小。视图选择合理,投影正确,布置得当。为了使加工**号易看懂、便于装配,图形尽可能与总装图一致,图形要清晰。
2、标注尺寸要求统一、集中、有序、完整。标注尺寸的顺序为:先标主要零件尺寸和出模斜度,再标注配合尺寸,然后标注全部尺寸。在非主要零件图上先标注配合尺寸,后标注全部尺寸。
3、表面粗糙度。把应用多的一种粗糙度标于图纸右上角,如标注"其余3、2。"其它粗糙度符号在零件各表面分别标出。
4、其它内容,例如零件名称、模具图号、材料牌号、热处理和硬度要求,表面处理、图形比例、自由尺寸的加工精度、技术说明等都要正确填写。
八、校对、审图、描图、送晒
(一)自我校对的内容是:
1、模具及其零件与塑件图纸的关系
模具及模具零件的材质、硬度、尺寸精度,结构等是否符合塑件图纸的要求。
2、塑料制件方面
塑料料流的流动、缩孔、熔接痕、裂口,脱模斜度等是否影响塑料制件的使用性能、尺寸精度、表面质量等方面的要求。图案设计有无不足,加工是否简单,成型材料的收缩率选用是否正确。
3、成型设备方面
注射量、注射压力、锁模力够不够,模具的安装、塑料制件的南芯、脱模有无问题,注射机的喷嘴与哓口套是否正确地接触。
4、模具结构方面
(1)分型面位置及精加工精度是否满足需要,会不会发生溢料,开模后是否能保证塑料制件留在有**出装置的模具一边。
(2)脱模方式是否正确,推广杆、推管的大小、位置、数量是否合适,推板会不会被型芯卡住,会不会造成擦伤成型零件。
(3)模具温度调节方面。加热器的功率、数量;冷却介质的流动线路位置、大小、数量是否合适。
(4)处理塑料制件制侧凹的方法,脱侧凹的机构是否恰当,例如斜导柱抽芯机构中的滑块与推杆是否相互干扰。
(5)浇注、排气系统的位置,大小是否恰当。
5、设计图纸
(1)装配图上各模具零件安置部位是否恰当,表示得是否清楚,有无遗漏;
(2)零件图上的零件编号、名称,制作数量、零件内制还是外购的,是标准件还是非标准件,零件配合处理精度、成型塑料制件高精度尺寸处的修正加工及余量,模具零件的材料、热处理、表面处理、表面精加工程度是否标记、叙述清楚。
(3)零件主要零件、成型零件工作尺寸及配合尺寸。尺寸数字应正确无误,不要使生产者换算。
(4)检查全部零件图及总装图的视图位置,投影是否正确,画法是否符合制图国标,有无遗漏尺寸。
6、校核加工性能
(所有零件的几何结构、视图画法、尺寸标'等是否有利于加工);
7、复算辅助工具的主要工作尺寸
(二)专业校对原则上按设计者自我校对项目进行;但是要侧重于结构原理、工艺性能及操作安全方面。描图时要先消化图形,按国标要求描绘,填写全部尺寸及技术要求。描后自校并且签字。
(三)把描好的底图交设计者校对签字,习惯做法是由工具制造单位有关技术人员审查,会签、检查制造工艺性,然后才可送晒。
(四)编写制造工艺卡片
由工具制造单位技术人员编写制造工艺卡片,并且为加工制造做好准备。在模具零件的制造过程中要加强检验,把检验的重点放在尺寸精度上。模具组装完成后,由检验员根据模具检验表进行检验,主要的是检验模具零件的性能情况是否良好,只有这样才能俚语模具的制造质量。
九、试模及修模
1、虽然是在选定成型材料、成型设备时,在预想的工艺条件下进行模具设计,但是人们的认识往往是不完善的,因此必须在模具加工完成以后,进行试模试验,看成型的制件质量如何。发现总是以后,进行排除错误性的修模。
2、塑件出现不良现象的种类居多,原因也很复杂,有模具方面的原因,也有工艺条件方面的原因,二者往往交只在一起。在修模前,应当根据塑件出现的不良现象的实际情况,进行细致地分析研究,找出造成塑件缺陷的原因后提出补救方法。因为成型条件容易改变,所以一般的做法是先变更成型条件,当变更成型条件不能解决问题时,才考虑修理模具。
3、修理模具更应慎重,没有十分把握不可轻举妄动。其原因是一旦变更了模具条件,就不能再作大的改造和恢复原状。
十、整理资料进行归档
模具经试验后,若暂不使用,则应该完全擦除脱模渣滓、灰尘、油污等,涂上黄油或其他防锈油或防锈剂,关到保管场所保管。
试模中常见问题 解决问题的方法与顺序
主浇道粘模 1抛光主浇道→2喷嘴与模具中心重合→3降低模具温度4缩短注射时间→5增加冷却时间→6检查喷嘴加热圈→ 7抛光模具表面→8检查材料是否污染
塑件脱模困难 1降低注射压力→2缩短注射时间→3增加冷却时间→4降低模具温度→5抛光模具表面→6增大脱模斜度→7减小镶块处间隙
尺寸稳定性差 1改变料筒温度→2增加注射时间→3增大注射压力→4改变螺杆背压→5升高模具温度→6降低模具温度→7调节供料量→8减小回料比例
表面波纹 1调节供料量→2升高模具温度→3增加注射时间→4增大注射压力→5提高物料温度→6增大注射速度→7增加浇道与浇口的尺寸
塑件翘曲和变形 1降低模具→2降低物料温度→3增加冷却时间→4降低注射速度→5降低注射压力→6增加螺杆背压→7缩短注射时间
塑件脱皮分层 1检查塑料种类和级别→2检查材料是否污染→3升高模具温度→4物料干燥处理→5提高物料温度→6降低注射速度→7缩短浇口长度→8减小注射压力→9改变浇口位置→10采用大孔喷嘴
银丝斑纹 1降低物料温度→2物料干燥处理→3增大注射压力→4增大浇口尺寸→5检查塑料的种类和级别→6检查塑料是否污染
表面光泽差 1物料干燥处理→2检查材料是否污染→3提高物料温度→4增大注射压力→5升高模具温度→6抛光模具表面→7增大浇道与浇口的尺寸
凹痕 1调节供料量→2增大注射压力→3增加注射时间→4降低物料速度→5降低模具温度→6增加排气孔→7增大浇道与浇口尺寸→8缩短浇道长度→9改变浇口位置→10降低注射压力→11增大螺杆背压
气泡 1物料干燥处理→2降低物料温度→3增大注射压力→4增加注射时间→5升高模具温度→6降低注射速度→7增大螺杆背压
塑料充填不足 1调节供料量→2增大注射压力→3增加冷却时间→4升高模具温度→5增加注射速度→6增加排气孔→7增大浇道与浇口尺寸→8增加冷却时间→9缩短浇道长度→10增加注射时间→11检查喷嘴是否堵塞
塑件溢边 1降低注射压力→2增大锁模力→3降低注射速度→4降低物料温度→5降低模具温度→6重新校正分型面→7降低螺杆背压→8检查塑件投影面积→9检查模板平直度→10检查模具分型面是否锁紧
熔接痕 1升高模具温度→2提高物料温度→3增加注射速度→4增大注射压力→5增加排气孔→6增大浇道与浇口尺寸→7减少脱模剂用量→8减少浇口个数
塑件强度下降 1物料干燥处理→2降低物料温度→3检查材料是否污染→4升高模具温度→5降低螺杆转速→6降低螺杆背压→7增加排气孔→8改变浇口位置→9降低注射速度
裂纹 1升高模具温度→2缩短冷却时间→3提高物料温度→4增加注射时间→5增大注射压力→6降低螺杆背压→7嵌件预热→8缩短注射时间
黑点及条纹 1降低物料温度→2喷嘴重新对正→3降低螺杆转速→4降低螺杆背压→5采用大孔喷嘴→6增加排气孔→7增大浇道与浇口尺寸→8降低注射压力→9改变浇口位置
塑胶模具设计中为什么有的地方要做镶件?既然是要做镶件,首先我们要对镶件有详细的了解:所谓的镶件是模具厂家口中的一种术语的叫法,但是这个叫法根据地方习惯不统一,有的称嵌件,有的呢习惯叫入子,它主要是镶在模仁中的模具的配件,形状也是跟模具配件的需要进行定做没有固定的形状,而且对对精密度的要求也是相对比较高的。
镶件的主要种类有:镶针,镶块,襄柱,还有镶圈等多种种类。镶件的主要材质有:SKD61、SKH51、ASP23、SKD11等多种材质,还有的是根据模仁的材料来匹配。镶件的硬度要求要在50HRC以上。它的标准的精度要求要在:±0.01mm,具体的要求还要根据模具的要求来定。
了解到镶件以后,模具厂家要在什么情况下需要对模具做镶件呢?
1,首先是想节省模具的材料:模具厂家在定模具料的时候都是形状比较规则的钢材材料,前模和后模的材料都是高点来决定,这个时候如果某一处的材料比较高,我们就可以做个镶件可以降低模仁的高度,这样就可以节省模具材料了。
2,方便以后模具出现问题进行改模:如果模具有需要经常修改的地方,我们就可以把它拆出来做一个或者是多个镶件,这样不仅方便我们修改模具还有备件替换。
3,有助于模具的排气:对于模具来说排气是比较重要的,如果排气不好模具的型腔内就会出现困气,这个时候注塑制品就比较容易出现气泡或者是收缩,或者是缺胶发白或者有黑点等一系列不良现象的出现。我们如果在需要排气的地方加上镶件,模具就可以利用镶件来进行缝隙排气。
4,方便模具的加工增加模具的使用寿命:我们在注塑模具中有时候会遇到比较深的骨位,这个时候刀具是很难加工的这个时候一般会采用做镶件的办法,降低加工的难度,不仅有利于排气还省了模具。一般情况下加镶件的地方都是比较容易坏的地方,这个时候我们只需要换点镶件就好,适当的增加了模具的使用寿命。
5,加上镶件之后可以传导模具的温度,正常来说模具都是通过设计水路来进行冷却,而有的地方到不了,我们就可以通过增加镶件进行散热,但是我们在选择镶件的材料时必须要选择热导性比较好的材料。
但是我们也不能只考虑优势而忽略了镶件的弊端:镶件增加了模具装配的难度,周围也容易产生溢胶飞边,有的时候也会增加塑胶模具设计的费用,在设计水路时会出现冲突,也会影响模具型芯的强度。
以上几点便是在塑胶模具设计中可以做镶件的地方,在我们利用镶件优势的同时,要注意加镶件的弊端,合理分配利用。
3.0模具设计的一般流程
1)1.模具确认表-总指标:交货期,模具寿命。
2.塑胶件:材料,表面质量,几何形状,其他要求。
3.注射机:型号规格。
4.行腔数目
5.行腔排布,模架确定、
6.分型面、
7.塑腔尺寸
8.主浇道以及分流道
9.浇口
10.冷却系统
11.结构件设计
12.行腔精确尺寸
13.**出系统
14.导向定位系统
15.排气系统
16.安装选件
2)对流程图的说明:
流程图只说明了在模具设计过程中考虑问题的先后顺序;而在实际的设计过程中可能并不是按此顺序进行设计的。并且设计中经常要再返回上步或上几步对已经的设计步骤进行修正,直至终决定设计。
4.0模架、内模材料的订制程序
1.主管
2.收到产品图 确认表
3.分析产品结构,模具设计要求
4.(1)复杂,安排画模具排位图
(2)简单,画模具结构简图
(3)客户要确认结构。 安排设计 客户确认。订料,调整设计
5.简单和复杂。 订模架。内膜大料。安排设计
6.之后审图
7.出图纸 明细表。
几点说明:
1) 收到不明确的产品图可以退回技术部,并加强与技术部代表沟通
2) 分析产品结构及模具设计要求要搞清注塑机吨位,然后选用适合注塑机的规格模架。对已定注塑机的规格要再确认。注射机锁模力>产品合模所需力≌注射压力×产品在分模面上投影面积=1吨/cm2×A。(上述1吨/cm2是一般情况下精确计算计参阅附录十一《常用塑胶材料一览表》根据胶厚、流程等选用注射压力)
计算锁模力后,还要计算所选注塑机射胶量是否合适,保证产品重量(折成体积)是射胶量(体积)的80%左右。
画结构简图前可以找一些相近模具设计文件夹作参考。
对不能明确认定的模架结构,可找相关人员协商定案。
开框图要以A4纸清晰表达。
安排画模具排位图要先向设计人员讲清大概思路,然后把产品图排入模架。排位图要画出内模大小、行位、运水等。排位图不须标尺寸,无须画顶针等,排位图要1:1打印出以方便审查,订料。
设计完成后应检讨已订材料是否与现设计一致,若有偏差应通知采购部作相应调整。
5.0塑件结构工艺性分析方法
5.1塑件工艺性分析的步骤:
塑件工艺性的分析包含五个方面的内容:
要分析塑件使用塑胶材料的成型工艺性能(包括流动性、收缩性、结晶性、定向作用、吸水性、硬化特征等)。
分析塑件的形状是否符合成型工艺和模具制造的要求。
要了解塑件使用场合及功能,把握塑件尺寸中的重点和关键点及外观面的位置和外观质量要求。
入水方式及入水点的形状会对塑件的终尺寸和形状产生影响。
对收缩率把握不准的场合,特别难控制的模具要预留收缩变动修模余量。
5.2塑件结构的要求
注射成型的塑件要合符注射成型的工艺要求及模具结构和制造尽可能简单的要求。
从注射工艺的要求析,塑件的结构应具备以下特点:
塑件的壁厚尽可能的均匀。壁厚有较大差别时,也用渐变去代替壁厚的突然变化。
塑件的壁厚要恰当,即不能过薄又不能过厚,一般在1 ~ 6mm范围内表2-3 是常用塑胶材料的壁厚值。
表2-3
塑料 小壁厚 小型塑件推荐壁厚 中型塑件推荐壁厚 大型塑胶件推荐壁厚
聚酰胺PA 0.45 0.75 1.6 2.4-3.2
聚乙烯PE 0.6 1.25 1.6 2.4-3.2
聚苯乙烯PS 0.75 1.25 1.6 2.4-5.4
改性聚苯乙烯HIPS 0.75 1.25 1.6 2.4-5.4
**玻璃PMMA 0.8 1.5 2.2 3.2-5.8
硬聚氯乙烯PVC 1.15 1.6 1.8 3.2-5.8
聚丙烯PP 0.85 1.45 1.75 2.4-3.2
聚碳酸酯PC 0.95 1.8 2.3 3-4.5
聚苯醚PPO 1.2 1.75 2.5 3.5-6.4
醋酸纤维素EC 0.7 1.25 1.9 3.2-4.8
聚甲醛POM 0.8 1.40 1.6 3.2-5.4
聚砜PSF 0.95 1.80 2.3 3-4.5
ABS 0.75 1.5 2 3-3.5
尽量使用圆角去代替尖锐的角,以利于塑胶的充模。
加强筋加快填充及增加壁件的强度和刚度。
一般原则是要求保证加强筋的大头尺寸,在(0.5-0.7)t的范围内,且加强筋大头的尺寸等于产品图筋位的名义尺寸。如果加强筋落在曲面上,且较深时,从制造的角度考虑应给出筋小头的尺寸。并且小头尺寸不应小于(表2-3)推荐的小壁厚,拔模角在10 ~ 50范围内给出。此时,如果大头的尺寸**出了产品图筋位的名义尺寸需要和技术部达成共识后调整。