廊坊浩北化工有限公司
联系人:缴克浩
电话:15613616888
地址:河北省廊坊大城县金地工业区
产品规格:
产品数量:
包装说明:
关 键 词:镇江锅炉脱剂厂
行 业:化工 化学助剂 精细化学品加工
发布时间:2023-03-17
钙增湿法
炉内喷钙加尾部烟气增湿活化脱工艺是在炉内喷钙脱工艺的基础上在锅炉尾部增设了增湿段,以提高脱效率。该工艺多以石灰石粉为吸收剂,石灰石粉由气力喷入炉膛850~1150℃
烟气脱工艺流程
烟气脱工艺流程
温度区,石灰石受热分解为氧化钙和,氧化钙与烟气中的二氧化反应生成亚。由于反应在气固两相之间进行,受到传质过程的影响,反应速度较慢,吸收剂利用率较低。在尾部增湿活化反应器内,增湿水以雾状喷入,与未反应的氧化钙接触生成氧化钙进而与烟气中的二氧化反应。当钙比控制在2.0~2.5时,系统脱率可达到65~80%。由于增湿水的加入使烟气温度下降,一般控制出口烟气温度**温度10~15℃,增湿水由于烟温加热被迅速蒸发,未反应的吸收剂、反应产物呈干燥态随烟气排出,被除尘器收集下来。
该脱工艺在芬兰、美国、加拿大、法国等国家得到应用,采用这一脱技术的大单机容量已达30万千瓦。
循环流化床法
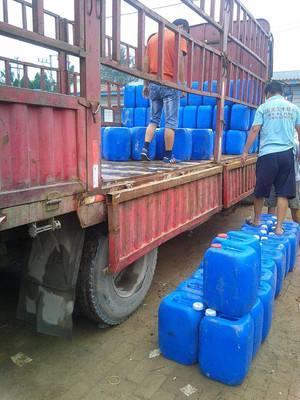
6、采用防腐工艺和材料,系统主设备寿命可达30年以上。
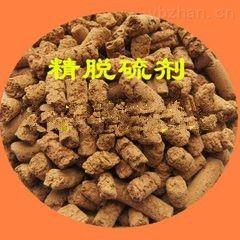
脱就是脱去烟气中的二氧化,脱硝主要是脱去烟气中的氮氧化物。这两种物质进入大气会形成酸雨,酸雨对人类的危害非常大,所以现在国家一直在提倡环保,以煤炭为燃料的烟气都含有这些物质,特别是火电厂,所以现在建火电厂的同时都要建设脱技术设备。
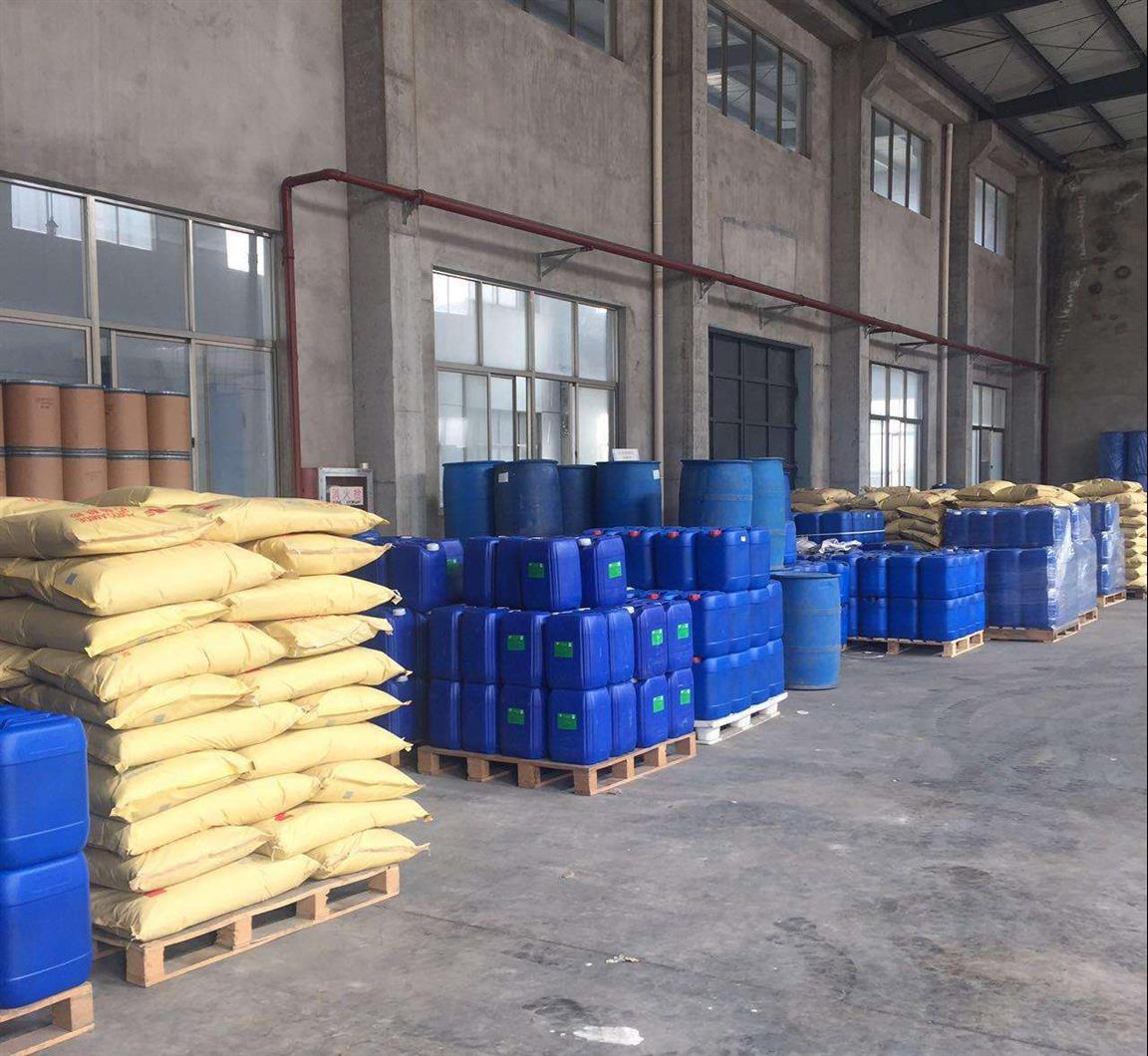
方法
编辑
除尘方法主要有电除尘、袋式除尘、旋流板湿式(麻石)除尘。脱方式主要有:炉内脱,烟气干式脱、烟气湿式脱等。采用干法处理设备庞大,投资大;经济和实用角度较常用湿法填料吸收塔、板式吸收塔、旋流板吸收塔等,
锅炉脱流程
编辑
1.运行时的技能要求脱除尘设备
1)留意易磨损部位如外筒内壁的变革。除尘设备 除尘器
2)含尘气体温度变革或湿度低落时留意粉尘的附着,堵塞和腐化现象。除尘器
3)留意压差变革和排出烟色状况,因为磨损和腐化会使除尘器穿孔和导致粉尘排放,于是除尘效率下降,排气烟色恶化,压差产生变革。
4)留意除尘器各部位的气密性,查抄旋风筒气体流量和集尘浓度的变革。
2.启动前的筹备事情
1)查抄各毗连部位是否毗连安稳.
2)查抄除尘器与烟道,除尘器与灰斗,灰斗与排灰装置,输灰装置等团结部的气密性,消除漏灰,漏气现象.
3)关小挡板阀,启动通风机,无异常现象后逐渐开大挡板阀,以便除尘器通过规定命量的含尘气体。
锅炉脱脱工艺
编辑
1、石灰石——石膏法烟气脱工艺
石灰石-石膏法脱系统流程
石灰石-石膏法脱工艺采用石灰石作为脱吸收剂,加水配成石灰石溶液。烟气直接进入主吸收塔,在主吸收塔内,石灰石浆液与烟气接触混合,烟气中的SO2与浆液中的石灰石发生一系列复杂的化学反应后被脱除,反应产物为亚采用强制氧化亚会被氧化成。脱后的烟气经除雾器除去烟气夹带的细小液滴后排入烟囱。吸收塔内的浆液排至亚曝气氧化系统,将亚氧化成。
锅炉烟气经过除尘器除尘后进入FGD,通过引风机引入吸收塔,吸收塔脱效率**95%。从吸收塔出来的净烟气温度约为50℃,通过烟囱排放。
本脱工程采用石灰石-石膏湿法脱工艺。以石灰石作为SO2的吸收剂,主要反应为烟气中的SO2先溶解于吸收液中,然后离解成H+和HSO3-,然后与加入的石灰石浆液反应,反应式如下:
SO2+H2O→H2SO3(溶解)
H2SO3⇋H++HSO3-(电离)
石灰石的主要成分是CaCO3,在溶液中,SO32-和HSO3-与CaCO3反应:
Ca2++CO32-+2H++SO42-+H2O→CaSO4·2H2O+CO2↑
2H++CO32-→H2O+CO2↑
CaSO3可加速石灰石的溶解。当吸收液的pH值控制得较低时(<5.5)循环吸收液形成了CaSO3和Ca(HSO3)2的混合物,该混合物以缓冲液的性质存在,使吸收的pH值保持相对平稳。
在塔内的浆液循环槽内,SO32-、HSO3-将通过充入空气进行强制氧化,其反应如下:
HSO3-+1/2O→ HSO4- (1)
HSO4- + H+ → SO42- (2)
石灰石-石膏法脱工艺以石灰石浆液作为脱剂,在强制氧化形成石膏。控制浆液氧化的pH值为5.5,氧化率95%以上,系统不会出现结垢堵塞现象,运行安全可靠。
特点:
(1) 集脱除尘一体化
烟气与脱液碰撞接触,经吸收、吸附等物化反应,同时去除烟气中的粉尘和二氧化,满足环保排放标准要求。
(2)运行费用低
采用吸收塔的设计,具有低液气比,低循环量特点,其脱剂及电耗较低。
(3)系统运行稳定
石灰石-石膏法是目前脱应用广、技术成熟工艺,系统运行稳定。
(4)脱效率高
采用吸收塔的设计,其脱效率大于95%。
(5)自动化水平高
脱剂添加、电动设备的启停、脱液控制等实现了自动化控制。显著降低了操作人员的劳动强度,改善了工作条件,提高了设备运行的稳定性。
2、旋转喷雾干燥烟气脱工艺
3、磷铵肥法烟气脱工艺
4、炉内喷钙尾部增湿烟气脱工艺
5、烟气循环流化床脱工艺
6、海水脱工艺
7、电子束法脱工艺
8、氨水洗涤法脱工艺