银川临工装载机油缸转斗动臂转向油缸报价 铲车配件厂家
价格:3950起
山东东上智能装备有限公司
联系人:孙中武
电话:18366666792
地址:山东省临沂市工程机械仓储园区
传统作业装置的更换方法须通过拆装销轴来进行,需要的拆卸和安装工具,熟练工人更换一次作业装置耗时在1?h以上。而配装快换装置的装载机则不同,驾驶员在驾驶室内操纵手柄,就能在作业现场完成各种作业装置的快速拆装,既保证了施工安全,又减少了拆卸安装时间,还能避免销轴在拆装过程中损坏。
齿轮泵窜油”,即液压油将骨架油封击穿而溢出。此现象普遍存在,主机厂反映强烈,齿轮泵窜油严重影响装载机的正常工作和齿轮泵的使用可靠性及环境污染。为利于问题的解决,现对齿轮泵油封窜油故障的原因和控制方法进行分析。
1 零部件制造质量的影响油封质量。如油封唇口几何形状不合格,缩紧弹簧太松等,造成气密性试验漏气,齿轮泵装入主机后窜油。此时应更换油封并检验材质及几何形状(国产油封与国外油封相比质量差距较大)。齿轮泵的加工,装配。如若齿轮泵加工,装配有问题,致使齿轮轴回转中心与前盖止口不同心,会造成油封偏磨。此时应检查前盖轴承孔对销孔的对称度,位移量,骨架油封对轴承孔的同轴度。
致使密封环产生裂纹和划伤,造成二次密封不严甚至失效,压力油进入骨架油封处(低压通道),因而油封窜油。此时应检查密封环材质及加工质量。变速泵的加工质量。从主机厂得到的反馈信息,与变速泵组装在一起的齿轮泵油封窜油问题较严重,因此变速泵的加工质量对窜油也有较大的影响。变速泵装在变速箱输出轴上,齿轮泵又通过变速泵止口定位而装在变速箱输出轴上,如果变速泵止口端面对齿轮回转中心的跳动**差(垂直度)。密封环材质及加工质量。此若存在问题也会使齿轮轴回转中心与油封中心不重合而影响密封。变速泵加工,试制过程中,应检查回转中心对止口同轴度及对止口端面的跳动。
CBG齿轮泵骨架油封与密封环之间的前盖回油通道不畅通,造成此处压力升高,从而击穿骨架油封。通过对此处改进后,泵的窜油现象有了明显的改善。2 齿轮泵与主机安装质量的影响齿轮泵与主机的安装要求同轴度小于0.05。通常工作泵安装于变速泵,变速泵又安装于变速箱。如果变速箱或变速泵的端面对花键轴回转中心的跳动**差,形成累积误差,致使齿轮泵在高速旋转状态下承受径向力,造成油封窜油。
部件之间的安装间隙是否合理,齿轮泵外止口与变速泵内止口及齿轮泵外花键与变速箱花键轴内花键,两者间隙配合是否合理,都对齿轮泵的窜油有影响。因为内,外止口属于定位部分,配合间隙不宜太大,内,外花键属于传动部分,配合间隙不宜太小,以干涉。
齿轮泵窜油与其花键滚键也有关系。由于齿轮泵轴外伸花键与变速箱输出轴内花健有效接触长度短,而齿轮泵工作时传递的扭矩较大,其花键承受大扭矩而发生挤压磨损甚至滚键,产生巨热,以致造成骨架油封橡胶唇口,老化,从而出现窜油。建议主机厂选用齿轮泵时应校核齿轮泵轴外伸花键强度,保证足够的有效接触长度。
3 液压油的影响液压油清洁度**差,污染颗粒大,各种液压控制阀及管道内的粘砂,焊渣等也是造成污染的原因之因为齿轮轴轴径与密封环内孔间隙很小,油中的较大固体颗粒进入其间,造成密封环内孔的磨损,划伤或随轴旋转,致使二次密封的压力油进入低压区(骨架油封处),造成油封击穿,此时应过滤或更换新抗磨液压油。
液压油粘度下降,变质后,油液变稀,在齿轮泵高压状态下,通过二次密封间隙的泄漏,由于来不及回油,引起低压区压力升高,从而击穿油封。建议定期化验油液,选用抗磨液压油。当主机大负荷工作时间过长及油箱油面较低时,油温可升高到100℃,致使油液变稀,骨架油封唇口老化,从而引起窜油,应定期检查油箱液面高度,避免油温过高。
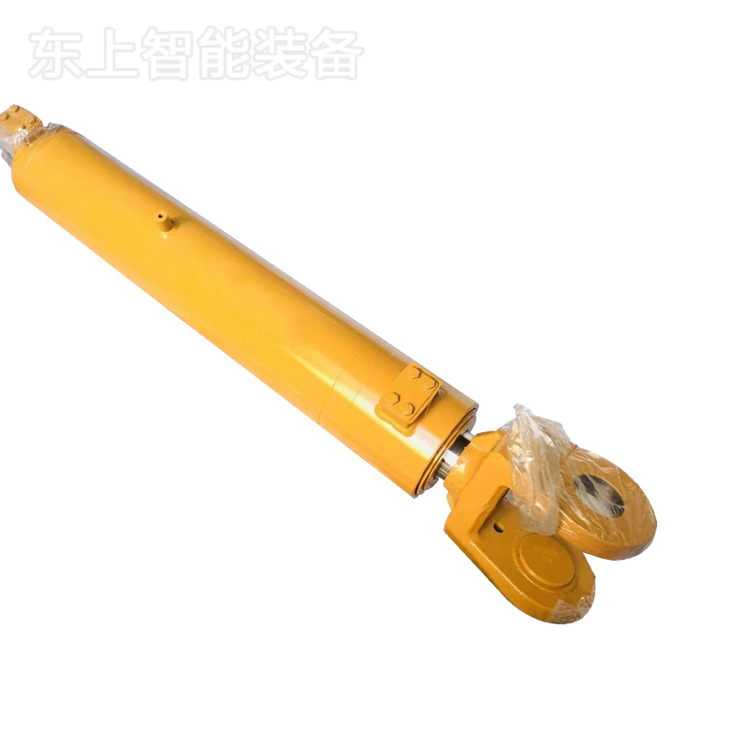
一辆ZL-50型轮式装载机在工作状态下易出现慢转向时转向较轻快,急转向时转向较低沉的现象。由于装载机工作时常采用急转向操纵以提高工作效率,转向沉会增加驾驶员的劳动强度,易使驾驶员疲劳,影响工作效率,所以装载机在大油门状态下应避免存在急转向沉的现象。针对转向沉的问题,对样机进行了慢转向,急转向过程中转向油缸压力的检测,转向压力均能达到规定的压力值。
转向力取决于轮胎与地面阻力矩的大小,通过转向液压系统的合理优化,反映在方向盘上的力及操作者所用的力为检测的转向力。该转向力的大小与转向器的流量有关,在低速转动方向盘时,转向器通过的流量取决于阀芯开启度的大小,随着转速增加,阀芯开启度逐渐,此时转向力较小,当达到转向器的 大流量时,即转向器阀芯完全开启,此时转向力为 小。要达到转向快与轻的效果,还取决于操作速度和流量的匹配。原因分析及排查根据装载机转向系统原理同时也取决于管路流量大小,当管径较小时,则起到节流阀的作用,严重时也能影响转向的速度和转向力的大小。
先检测转向系统压力是否达到规定值。经检测,转向压力均能达到规定的压力值,这说明不是压力原因造成的急转向沉。除此外,只可能是供油速率低造成被动转向而导致急转向沉,即急转向时由于向转向油缸提供的压力油速率不能满足急转向时所需的油量,从而导致急转向沉。
对转向系统液压元件分析后,认为造成液压转向系统急转向供油速率低的原因有以下几点:转向液压系统存在空气,液压油箱油位低,泵吸油量不充分,滤芯堵塞,使液压油箱油液流动不通畅,导致泵吸油困难,**阀阀芯卡住,不能完全打开。
使用的转向器排量不够,转向泵的排量不够,转向管路通径太小。针对以上原因,对故障原因进行逐一排查:液压系统排气处理:将转向器打到限位置,憋压,使液压管路气体通过油箱排出,将左转向油缸大腔的放气螺栓拧开,然后左转向,将左油缸大腔的气排除,同样的方法排查小腔的气体及另一油缸内的气体。
将液压油加至规定位置,清洗滤芯,清洗**阀,对转向器排量进行查对,对转向泵排量进行核对。经过以析及排查后,仍未解决转向沉的问题,说明管路通径偏小是造成急转向沉的主要因素,决定加大转向管路通径,故障得以排除。
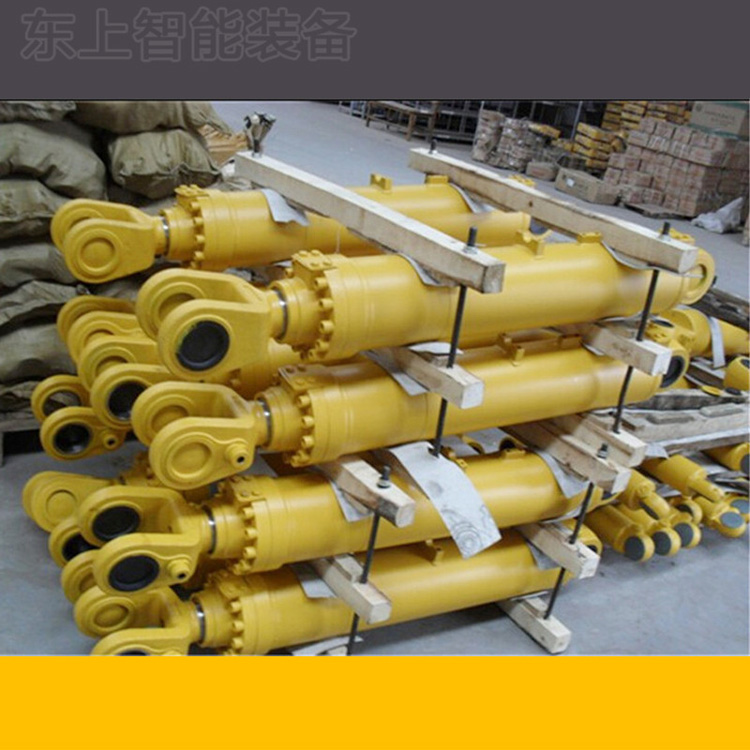
上下盖板及各板等件组成。腹板和上盖板是下较后分别需经两次成型而转入焊接的,我公司板材成型是采用冷压法成型,因而受成型条件限制以及成型 的不稳定待因素的影响,使腹板与上盖板接合和的空间曲线形状贴合间隙 大可达25mm,为焊接工序带来了很大的困难。况且间隙过大,焊接时只能采用加塞铁皮的办法来进行人工施焊,焊接机器人无法得到充分的使 用,这样不仅降低了焊接机器人的利髟率,而且使焊接强度也受到较大的影响。原后车架存在的缺陷原后车架结构主要缺陷有以下三方面:后铰接架部分主要由左右腹板多年来,我们在成型工艺,模具上做了大量工作,但效果都不太理想。
副车架支承架的悬泅为成型件结构,其工艺流程为:下料→钻孔→成型→铣两端面→焊接。不仅工序繁多,增加生产成本,而且成型时易出现微裂纹,使其强度也受到一定的影响。焊缝的位置不合理,尤其是副车架支承架的两侧钢板与中侧板连接处,焊接时容易引起应力集中,造成每年至少有5-7台的后车架在此位置断裂,直接经济损失达5万余元。
新型后车架的结构特点针对以上存在的问题,我们对原后车架进行了设计改进,它具有以下四个方面的特点:后铰霎架部分的腹板和上盖板改为一次成型件,这样其接合处为一平面曲线,成型简单且易保证。组焊时腹板与上盖板的贴合间隙较小,并且焊接工艺性较好。
副车架支承架的悬梁改为直接下料非成型件结构,不钗省去了成型铣加工两道工序,降低了生产成本,而且避免了成型时裂纹产生,提商了车架的强度。副车架支承架的铰接孔由轴套式改为贴圆盘式,不仅省去了轴套等零件,而且降低了生产成本,提高了劳动生产率。
调整改变了后车架的焊缝位置,副车架的两侧钢板由矩形改为斜口状,这样避免了与中侧板焊缝 处和应力集中,改变了焊缝的受力状况,提高了车架的抗拉和抗弯曲强度。改进效果新型后车架的制作和使用,不仅解决发多年来的腹板与上盖板接合处间隙过大,焊接工艺性差有难题,主要体现在以下几方面。
新型后车架的焊接工艺好由于避免了曲面间的接合,无论是人工焊接还是采和机器人焊接都较原后车架施焊方便,劳动强度低,效率高,并且焊缝布置合理,避免了应力集中,提高了车架的强度。新型后车架的成本较低与原后车架相比,淡仅省去了腹板,上盖板的一次成型,悬梁的成型和铣加工两道工序,轴套等一些零件,**每年即可为公司节约成本费16万余元,而且减少了零部件的工序周转,降低了劳动强度,提高了劳动生产率。后车架的结构通用性较强 稍作改动即可适用ZLZL60装载机的后车架,对其它类型装载机的后车架也具有,较强的借鉴作用,。
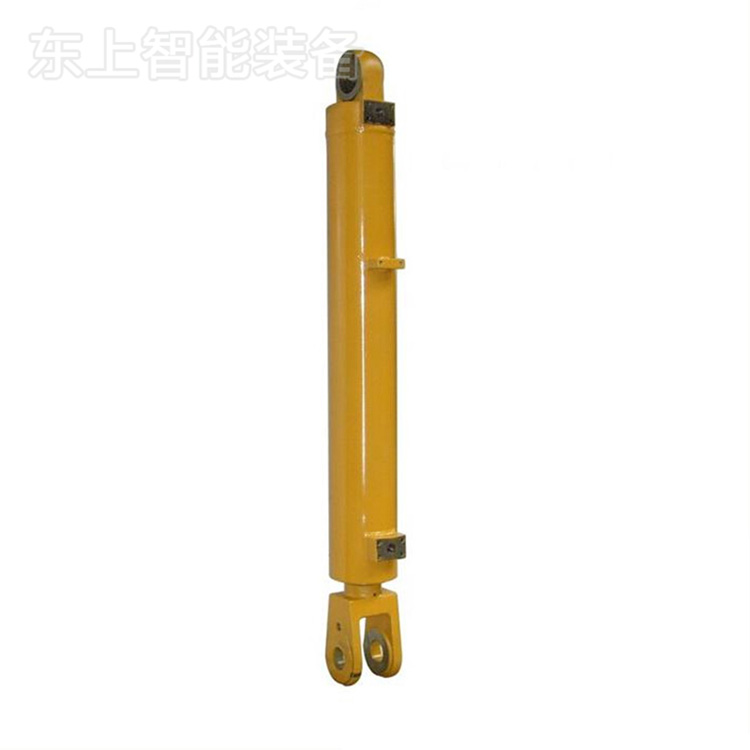
主减速齿轮长期工作磨损造成啮合点不好,使主减速齿轮行驶时有响声,轴承磨损**过期限或轴承松动导致行驶时有响声,齿轮磨损过大,行驶时有响声。制动时发响,主要是由于制动底板弯曲变形,制动摩擦片铆钉松动和制动鼓损坏等导致驱动桥制动时发出响声。制动时车跑偏。由于装载机工作时间过久不可避免地使驱动桥的制动蹄表面粘上了油污,使制动力减小,因而使制动时出现车跑偏现象,再有制动间隙调整不当,亦可造成制动时车跑偏现象。驱动桥工作异常。行驶时有响声。主要原因有三点另外,轮胎的气压不足,已经不符气压标准,出现两侧轮胎气压不一致时,就导致出现制动时车跑偏故障现象。制动失灵。主要是由于制动鼓与制动蹄间隙调整不当或有油污,或制动摩擦片磨损**限,都能导致制动失灵。
多路阀阀杆间隙过大都有可能造成动臂举升后自行下沉。油浸过高。 主要的是两个原因造成的,一个是重负荷工作时间过长,一个是油量不足。 后才导致的油温过高的现象。方向盘回位后仍继续转向。这是一个其危险的故障。主要原因,由于转向器内四位弹簧片损坏导致方向盘回位后仍然继续转向,由于配油套和配油轴之间卡死或配油套与阀体之间卡死,导致了方向盘回位后仍继续转向。脚制动力不足。共存在六个原因,即制动分泵漏油。
液压系统压力低,造成了动臂提升力不足或转斗力不足,吸油管及滤油器堵塞使油路不畅导致动臂提升力不足或转斗力不足,油泵,油缸,管路内漏等原因也可以造成动臂提升力不足或转斗力不足,多路阀过度磨损,阀杆与阀体配合间隙**过规定值使动臂提升力不足或转斗力不足。液压制动系统工作性能减低或不稳定主要原因有:工作油变质,有异物进人或堵塞管路,滤油器堵塞或损坏,系统内产生空气等都可导致液压制动系统工作性能减低或不稳定。液压制动系统故障。动臂提升力不足或转斗力不足。主要是因为安全阀调整不当动臂举升后自行下沉。原因是动臂油缸的内漏制动液压管路中有空气,制动总泵皮碗损坏,制动总泵油液不足,推杆行程调节不当,制动摩擦片磨损到限。
导致蓄电池不充电或充电率低,发电机皮带过松或损坏,导致蓄电池不充电或充电率低,接线不牢,接触不良,导致蓄电池不充电或充电率低,调节器调节不当或有损坏,导致蓄电池不充电或充电率低。蓄电池容量不足。电解液比重或液面过低,板间短路,板磁化,导线接触不良,板活性物质脱落等等,均可导致蓄电池容量不足。发电机不发电。主要原因剩磁消失,磁场线圈断路,整流子接触不良,电住不灵活,电枢匝间短路。电气系统不正常。发电机正常而蓄电池不充电或充电率低。蓄电池板磁化这些原因的每一种原因均可导致发电机不发电。
装载机平稳换挡的关键零件是弹簧蓄能器和主压力阀。其工作原理:蓄能器端部的活塞装在活塞缸内,右端**在弹簧上,大小弹簧右端分别**在主压力阀和壳体的凸台上。活塞左端与端部的螺塞间形成油室A,并通过油道与换向阀的连通油道相通。在这段油道上装有单向阀和节流孔。换挡时油路的液压流入换挡离合器的油缸,从而使油路中油压降低,蓄能器油室A的油室经单向阀补充油液,使制动器或离合器迅速结合。同时由于油室A的油流出,在主压力阀控制油道(a-b)的作用下,阀杆左移使系统的油压下降,当主、从动盘贴紧时,油缸停止移动,油压上升,一部分油液经节流孔流向油室A,油室A的压力逐渐升高,推动活塞右移,压缩弹簧,主压力阀的阀杆右移,这样系统的油压便逐渐升高,使主、从动部件结合平稳,实现平稳可靠换挡。