产品规格:
产品数量:100000 个
包装说明:
关 键 词:gmp车间车间
行 业:环保 净化工程
发布时间:2023-02-13
中净环球净化可提供GMP车间、无菌车间的咨询、规划、设计、施工、安装、改造等配套服务。技术专业、经验丰富、价格实惠。拥有装饰装修、机电安装、净化行业设计。
风管和附件
1.风管断面尺寸应满足对内壁清洁处理的要求,并宜设置清扫口。风管应采用不易脱落颗粒物质、不易锈蚀,且耐消毒的材料。
2.净化空气调节系统应按需要设置电动密闭阀、风量调节阀、防火阀、止回阀等附件。各医药洁净室的送风、回风管段应设置风量调节装置。
3.下列情况的通风、净化空气调节系统的风管应设置温度为70℃的防火阀:
3.1穿越防火分区处;
3.2穿越通风、空气调节机房的房间隔墙和楼板处;
3.3穿越重要或火灾危险性大的场所的房间隔墙和楼板处;
3.4穿越防火分隔处的变形缝两侧;
3.5竖向风管与每层水平风管交接处的水平管段上。
4.服务于爆炸危险场所的风管穿越甲类、乙类生产区的隔墙或防爆隔墙时,应设置防火阀和止回阀。厂房内用于有爆炸危险场所的排风管道,严禁穿过防火墙和有爆炸危险的房间隔墙。
5.医药洁净室净化空气调节系统的风管和调节阀,以及空气过滤器的保护网、孔板和扩散孔板等附件的制作材料和涂料,应根据输送空气洁净度级别及所处空气环境条件确定。
6.医药洁净室内排风系统的风管、调节阀和止回阀等附件的制作材料和涂料,应根据排除气体的性质及所处空气环境条件确定。
7.用于医药洁净室的送风管、排风管、风阀及风口的制作材料和涂料应耐受消毒剂的腐蚀。
8. 在空气过滤器前、后应设置测压装置。在新风管、送风、回风和排风总管上应设置风量测定装置。各系统末端的空气过滤器均应设置检漏孔,且各系统末端空气过滤器设置的压差计不宜少于2个。
9.风管、附件及材料的耐火性能,应符合现行标准《洁净厂房设计规范》GB50073的有关规定。
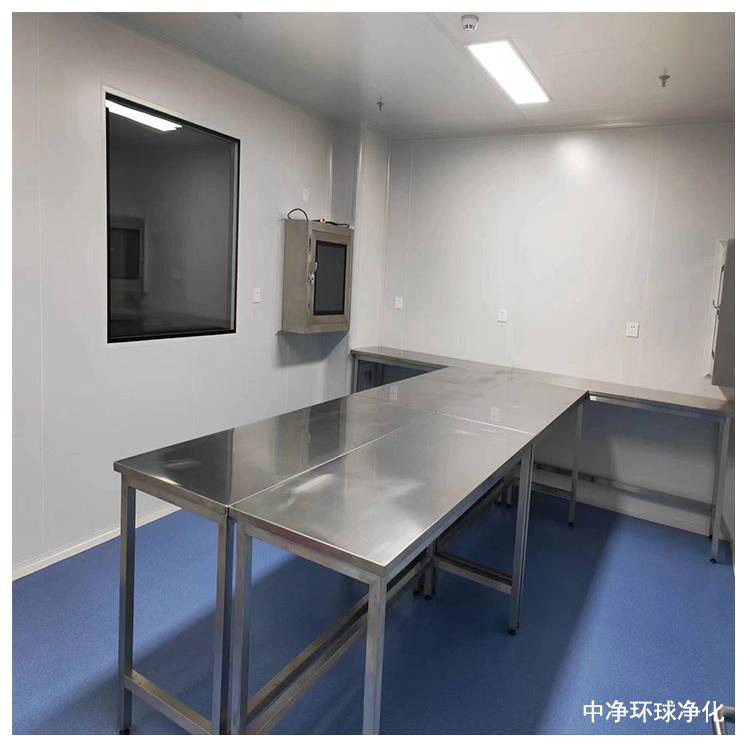
GMP厂房的规划设计要求
一、GMP生产工厂的厂址选择,应根据下列原则,并经技术经济方案比较后确定:
1.应在大气含尘、含菌浓度低,无有害气体,自然环境好,对产品质量无有害因素,卫生条件较好的区域。
2.应远离铁路、码头、机场、交通要道以及散发大量粉尘和有害气体的工厂(如化工厂、染料厂及屠宰厂等)、贮仓、堆场等有严重空气污染、水质污染、振动和噪音干扰的区域。如不能远离严重空气污染区,则应位于其大频率风向上风侧,或全年小频率风向下风侧。
3.排水良好,应无洪水淹没危险。
4.目前和可预见的**区域规划,不会使厂址环境产生不利于产品质量的影响。
5.水、电、燃料、排污、物资供应和公用服务条件较好或所存在的问题在目前和今后发展时能有效、妥善地解决。
二、GMP生产工厂的总平面布置(即总图)应根据下列原则,并经技术经济方案比较后确定:
1.GMP生产工厂的总平面布置在遵循有关工业企业总体设计原则外,还应按照不对药品生产产生污染,营造整洁的生产环境的原则确定。
2.生产、行政、生活和区的总体布局应合理、不得互相妨碍。
3.生产厂房应布置在厂区环境清洁区域,厂区的地面、路面及运输不应对药品的生产造成污染。
4.药品生产厂房与**交通干道之间距离不宜小于50m。
5.对于兼有原料药和制剂的药厂,应考虑产品的工艺特点和防止秤时交叉污染,合理布局、间距恰当。原料药生产区应置于制剂秤区的下风侧,青生产厂房的设置应严格考虑与其他产品的交叉污染。
6.在符合消防和尽量减少互相交叉污染的原则下,宜减少立厂房幢数,建立联合厂房,以减少厂区道路及其造成的污染,减少厂区运输量和缩短运输线路。但生产青类等高致敏性药品必须使用立的厂房与设施;避孕药品的生产厂房应与其他药品生产厂房分开;生产用菌毒种和非生产用菌毒种、生产用细胞与非生产用细胞、强毒与弱毒、死毒与活毒、脱毒前与脱毒后的制品和活疫苗与灭活疫苗、人血液制品、预防制品等的加工或灌装不得同时在同一生产厂房内进行,其贮存要严格分开。
7.危险品库应设于厂区位置,并有防冻、降温、消防措施;和剧品应设仓库,并且防盗措施。
8.动物房的设置应符合颁布的有关规定,并有的排污和空调设施。
9.厂区布置和主要道路应贯彻不流与货流分流的原则,尽量避免相互交叉。厂区道路面应选用整体性好、灰尘少的材料,如沥青、混凝土。厂房与道路之间应有一定距离的卫生缓冲带,缓冲带可种植草坪,严禁种花,树木周围以卵石覆盖土壤,绿化设计做到“土不见天”。
10.厂房周围宜设环形消防车道(可利用交通道路),如有困难时,可沿厂房的两个长边设置消防通道。
11.GMP生产厂房周围不宜设置排水明沟。
12.车辆的停车场应远离药品生产厂房。
13.生产废弃物的回收应立设置。
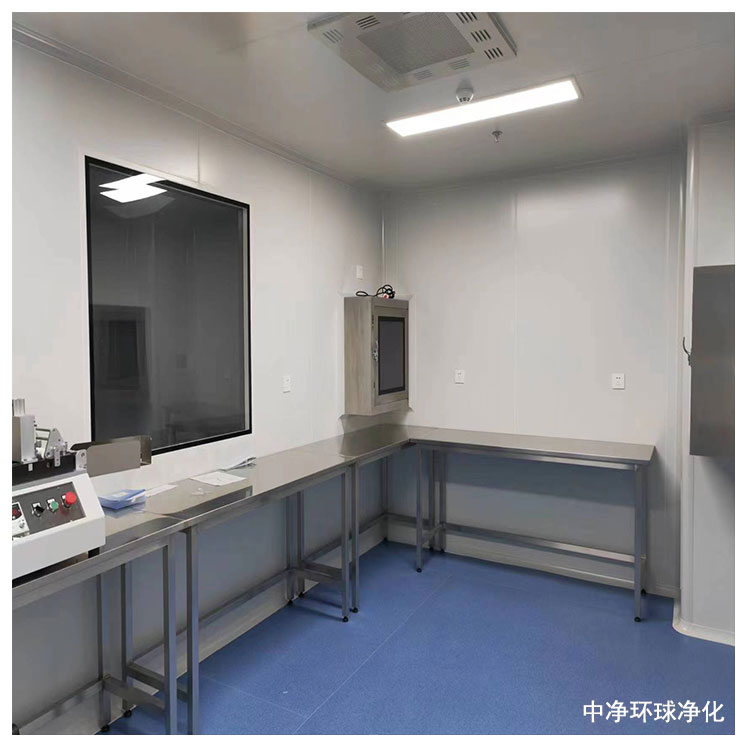
湿法干法制粒工艺验证要点分析
文章摘自药品GMP指南2010,与片剂干混直接压片的一般工艺比较,湿法制粒增加了两个黄色背景标出的工序(制粒-干燥),包括称量-过筛-制粒-干燥-混合-分料-压片-包衣(充填)几个工艺步骤。
同样,在湿法制粒过程中,也需要考虑到批量的影响,批量大小往往是验证的关键参数之一。此外,制粒机切刀和搅拌的速度,添加粘合剂的速度、方法,投料的顺序以及制粒终点的判定也决定着终产品的粒度;对于部分原料药含量比较低的情况,原料投料的顺序也很关键;达到制粒终点后,整粒方式与筛网尺寸,出料方法对终的粒度也有可能会有影响。
在湿法制粒的工序中,粒度的分布情况,水份含量,松紧度等往往会是重要的考察指标。对于制粒的终点电流值,往往可以通过PAT(过程自动控制技术)去判断。
干燥的工序其实在包衣工序中也有涉及,所要求的关键工艺参数也基本类似,进风温度、湿度和风量以及出风温度,产品的温度,干燥时间,干燥后颗粒的水份往往会是关键工艺参数,这些参数往往会影响到的CQA是水分。
与片剂干混直接压片的一般工艺比较,干法制粒增加了两个黄色背景标出的工序(辊压-整粒),并且整粒后的混合工序与常规的混合略有差异,包括称量-过筛-混合-辊压-整粒-混合-压片-包衣(充填)几个工艺步骤。
辊压与整粒工艺参数包括自动模式;辊压压力;进料速度;薄片厚度;真空压力;筛网孔径;辊压表面等工艺参数。GMP指南中将辊压夹角定义为了考察指标,这点有些无法理解,其他的考察指标包括堆密度、薄片强度,颗粒可压性等均可以理解。(希望有熟悉干法制粒的朋友们补充解释一下,这个辊压夹角从字面上感觉像是设备设定,而并非制粒的指标)
在混合的工艺步骤,混合均匀度仍然是考察的重要指标,影响这个重要指标的参数包括但不限于,混合速度,批量,加料和出料方式,体积比以及混合时间。
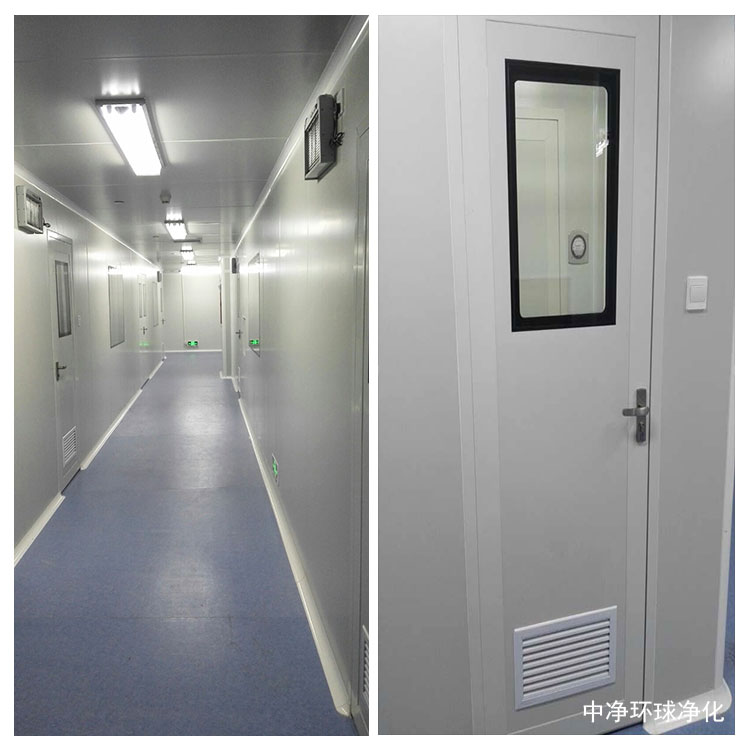
气流流型和送风量
1.气流流型的设计应符合下列规定:
1.1气流流型应满足空气洁净度级别的要求,空气洁净度为A级时,气流应采用单向流流型。
1.2空气洁净度为B级、C级、D级时,气流应采用非单向流流型。非单向流气流流型应减少涡流区。
在混合气流的医药洁净室内,气流流向应从该空间洁净度较高一端流向略低一端。
1.3医药洁净室气流分布应均匀。气流流速应满足生产工艺、空气洁净度级别和人体卫生的要求。
2.医药洁净室气流的送风、回风方式应符合下列规定:散发粉尘或有害物质的医药洁净室不应采用走廊回风,且不宜采用**部回风。
3.医药洁净室内各种设施的布置,除应满足气流流型和空气洁净度级别的要求外,尚应符合下列规定:
3.1单向流区域内不宜布置洁净工作台,在非单向流医药洁净室内设置单向流洁净工作台时,其位置宜远离回风口;
3.2易产生污染的工艺设备附近应设置排风口;
3.3有局部排风装置或需排风的工艺设备,宜布置在医药洁净室下风侧;
3.4有发热量大的设备时,应有减少热气流对气流分布影响的措施;
3.5余压阀宜设置在洁净空气流的下风侧。
4.医药洁净室的送风量应取下列各项计算所得的大值:
4.1维持洁净度级别要求所需的送风量。送风量根据室内产生的微粒数计算确定。
4.2维持洁净度级别所需的“恢复时间”确定的送风量。
4.3根据室内热湿负荷计算确定的送风量。
4.4向医药洁净室给的新鲜空气量。